The State of Indiana, BSA LifeStructures and Pepper took a highly-integrated approach during design that continued into construction and extended to every person on the project.
The team developed a plan to educate everyone working onsite about the role they had in the safety of future patients and hospital staff.
"With the challenge of getting everyone to understand the mission and unique aspects of construction, we knew it was important to educate trades not only on what they were doing but also why."
Augie Ziccarelli, Senior Project Manager
From laminated safety glass and radiused wall corners to behavioral health grade furnishings, the construction team served as the last line of defense, checking the documents and ensuring the proper systems and materials were installed.
How would we guarantee 34 state-contracted prime contractors would adhere to the strict requirements and regulations necessary to translate the design into a safe reality?

Influencing patient behavior
- Pastel nature murals
- Programming tunable lighting
- Interrupting sight lines in mixed populations
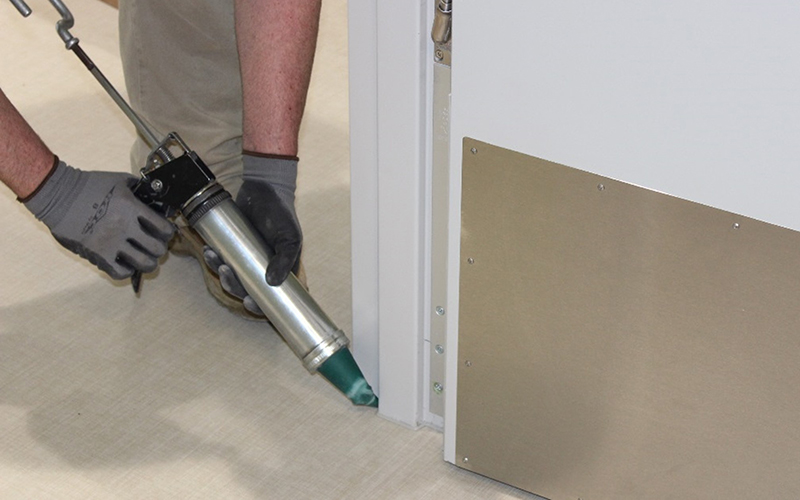
Protecting patients and staff
- Anti-ligature fasteners
- Security sealants
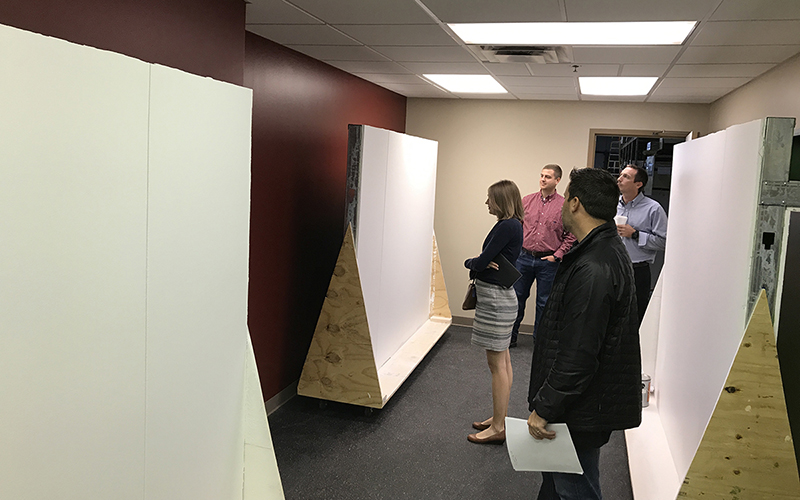
Building durability and maintenance
- Fiberglass-faced drywall
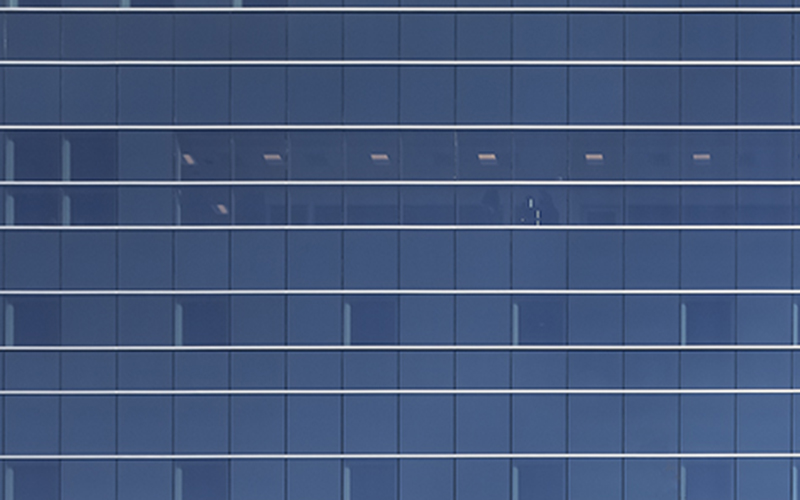
Controlling building logistics
- Elevator programming & controls
- Electrochromatic glass
Creating a culture of caring and empathy made every trade partner an expert and advocate for achieving the highest level of quality and safety, regardless of their contract or previous experience.
- Every tradesperson was required to participate in a project-specific orientation, where they learned about the facility and risks to patients and staff from improper installation.
- The importance of using specific materials for certain areas was stressed and reinforced with safety bulletins throughout the site.
- Tying Pepper's role into the goals was important for us to understand the atypical needs of the facility.
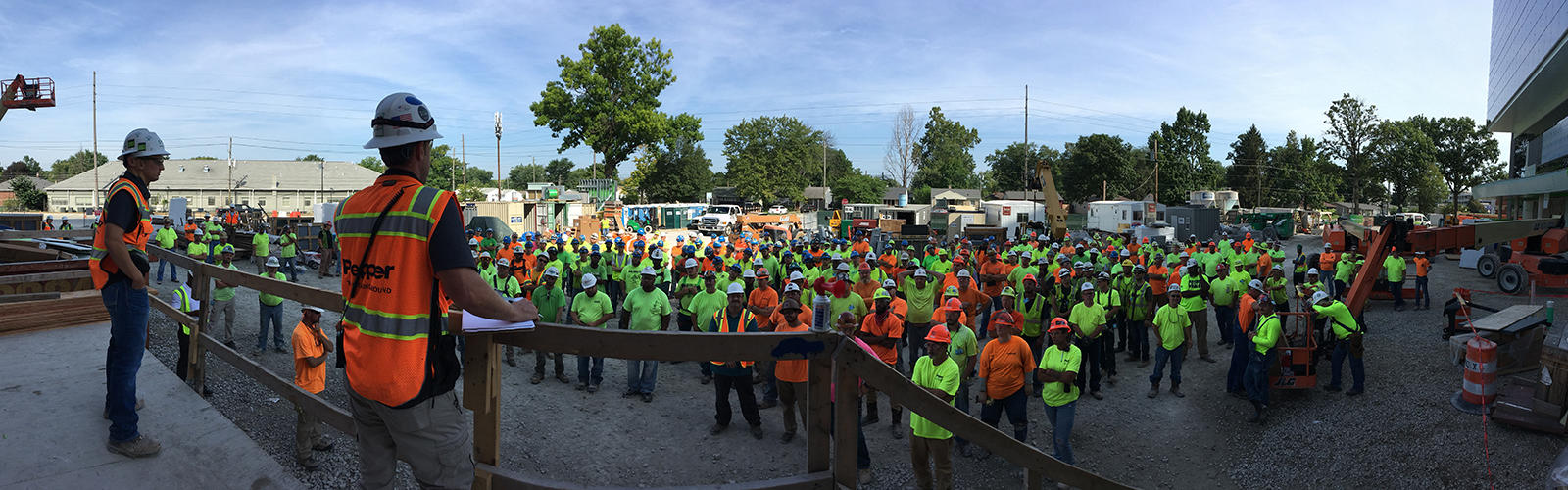
Every screw and surface mattered
The team focused in on the safety of the building itself. It wasn't enough that the drywall was smooth; the finish had to be like glass. A single screw left inside a wall could be deadly for future patients and staff. Inspiring the trades to care about the quality of their work and speak up when something seemed amiss required extra effort.
"We stressed to the tradespeople how important it was to clean up after themselves. Not one drawer could have a loose screw. If one screw was missed, it could result in serious injury to a patient or staff member."
Chris Conover, senior Project manager
Pepper met with the owner to learn why the materials were used. What incidents happened in the past? What should they share with the trades to convey the importance of their work? FSSA shared real stories about patients who hurt themselves and staff, from ingesting materials to using loose screws and exposed edges as weapons.
The project team incorporated these stories into the jobsite safety orientations and bulletins, with the goal of empowering everyone onsite to monitor for safety. Trades were asked to look for sharp corners that should be rounded, ensure security fasteners were used and that screws were not left exposed.
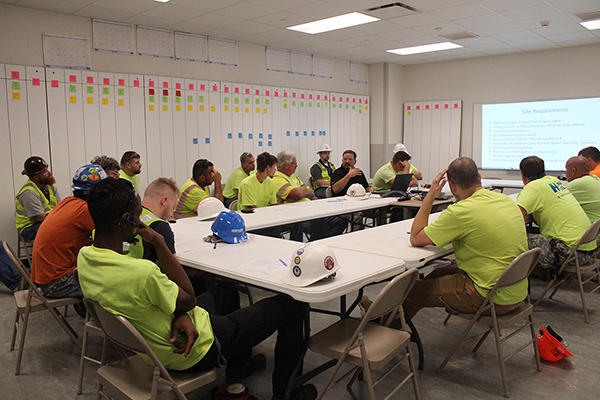
Gaming technology saves the schedule
Early in the project, traditional methods were creating some delays in the schedule. The building's framing was scheduled to go up before the ductwork was installed, and as tradespeople installed the ductwork, they encountered issues with the layout of framed openings.
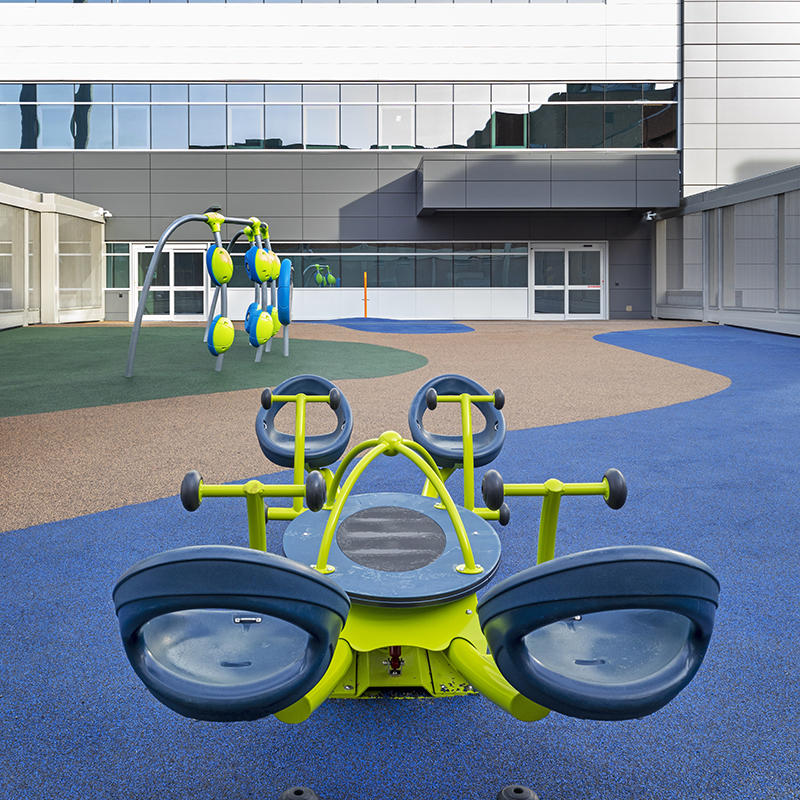
A creative quality control solution
Later, Pepper's problem-solving skills were put to the test in a different way with the rooftop playground. As we were mocking it up, a constructability issue surfaced with regard to the architectural metal fence.
Cutting the steel created a sharp edge. The team brainstormed and found their solution in an unlikely place - a car website. A hard rubber edge was incorporated into the bottom of the fence.
Preparing staff for their new space
As the project neared completion, the team helped with the transition. Using the design model, Pepper put together a video orientation that walked staff through the space, giving them an idea of what to expect before they arrived on their first day. It was a simple activity that made a difference.
To further enhance the FSSA's ability to maintain its new facility, the owner decided to invest in a 3D facility management (FM) deliverable. The chosen platform allows the hospital to update maintenance records, track trends and tie field work orders to their building management system - telling them what rooms and systems could be affected downstream, which will be beneficial in avoiding interruptions to patient care.
Tour the finished space.
NDI opened on March 15, 2019.