Indiana NeuroDiagnostic Institute and Advanced Treatment CenterHealthcare, Quality, Industry insights
After a decades-long trend to deinstitutionalize psychiatric patients, society is slowly making changes to address the unmet needs of the nearly 44 million Americans dealing with mental health issues. As states and healthcare providers take steps to address the mental health crisis, the contractors who build the facilities need to also bring a different kind of care to the table.
Approaching the job with empathy helps individual workers grasp the risks involved with these spaces, and that requires understanding that healthcare isn't mental health care, but mental health care is healthcare.
What does that mean?
It means that while behavioral health facilities have some of the same general needs as other medical facilities, they also require assessing and addressing their atypical needs. That's truer than ever now that providers are moving toward more personalized approaches to treating mental health.
Pepper's experience in the healthcare industry covers all specialties and functions of a hospital. Still, our experience renovating behavioral health units and recent construction of the new Indiana NeuroDiagnostic Institute and Advanced Treatment Center (NDI) required understanding the unique challenges and needs of patients, staff and the facility. The biggest difference we see between behavioral health construction and acute care space is the emphasis on building safety, even over medical systems, Interim Life Safety Measures and Infection Control (though they are all still important).
Understanding the risks of behavioral health construction
Considering 1 in 5 adults in America experience a mental illness, rates for depression among youth are on the rise and countless communities are reeling from an opioid crisis, we get there isn't a clear-cut picture of what a "typical" mental health patient looks like. While there is no one-size-fits-all treatment, and behavioral health facilities treat an array of afflictions, age groups and risk levels,. one common denominator is that patients may look for ways to use their surrounding environment to harm themselves or others.
Just as in any healthcare setting, if work is happening in or around an existing space, keeping current patients and staff safe should be a top priority. And particularly in a medical center that houses a psychology unit on one floor or in a small portion of the building, those working in the building need to understand the constraints staff have treating a broad spectrum of conditions within a limited space.
Understanding the risks and collaborating to find solutions is critical for the construction manager (CM) or contractor to build a safer facility for patients and staff. That engagement empowers us to make informed decisions in everything from the selection of materials to the type of installation to securing every individual space.
Engagement is key
How do you mitigate the risks? By keeping everything patient-centered. From our experience, a high level of transparency and communication across the project results in powerful side-by-side collaboration. Take NDI as an example:
At the start of the project, we sat down with the owner, Indiana's Department of Family and Social Services Administration and designer BSA LifeStructures and asked a series of questions:
• How old are the patients?
• What behavioral issues may they be dealing with?
• How could they possibly harm themselves?
• How could they possibly harm staff?
• How could the building be used to do so?
• What materials could patients transform into a weapon?
During conversations, the owner was clear about the needs of the diverse group the hospital would inevitably serve – men, women and children with various risk levels and afflictions, including post-traumatic stress disorder, schizophrenia, autism, opioid addiction and more. They stressed how these vulnerable patients are often subject to quick diagnoses in a short-term doctor's visit or placed in long-term custodial or out-patient care. NDI, however, aimed to help patients over a period of time through true observation, proper diagnosis and, if needed, a long-term plan. Tying our role as the construction manager into the goals was important for all of us to address the atypical needs of the hospital.
Once everyone is on the same page, incorporating the following measures into the construction process helps those installing the work understand their role in the end user's safety and become an active participant in monitoring for potential hazards.
Leveraging mockups to confirm anti-ligature
A lot of recognition goes to the design of new behavioral health facilities, but the attention to detail doesn't stop there. Once design is nearing completion, you need to create a bridge from the design intent to actual constructability with safe material selection – all with patient and staff needs in mind.
One of the most critical things to consider when building a space for people dealing with mental health issues is whether the space has ligature points where sheets, cords, towels, rope or some other material can be looped or tied to a fixture. Standard items such as beds, faucets, showerheads, doors and light fixtures can easily become a ligature risk, resulting in potentially life-threatening situations for patients.
It's not enough that owners and architects know this. Construction teams also need to familiarize themselves with the risks and seek anti-ligature products that are functional yet safe for patients and staff. One of the most effective ways to validate the safety of materials, whether it's anti-ligature products or building materials, is to use a side-by-side combination of virtual mockups and physical mockups.
For the NDI project, Pepper, the owner and the designer worked with more physical mockups than we would on other healthcare projects. Everything from paint, drywall, caulk, screws, signage, artwork and any other aspects of the design that would be exposed to patients were evaluated and tested. By maneuvering potential beds, signage, plumbing and other fixtures, we were able to assess the safety of products and make alterations in advance for high-risk units.
Not only does planning ahead raise the level of quality and prevent rework, but that extra attention to detail could ultimately save lives.
Engaging trades in the hospital's mission
With patient and staff safety at the top of the priority list during design and preconstruction, how do you ensure trade partners execute their work with that same level of care during construction?
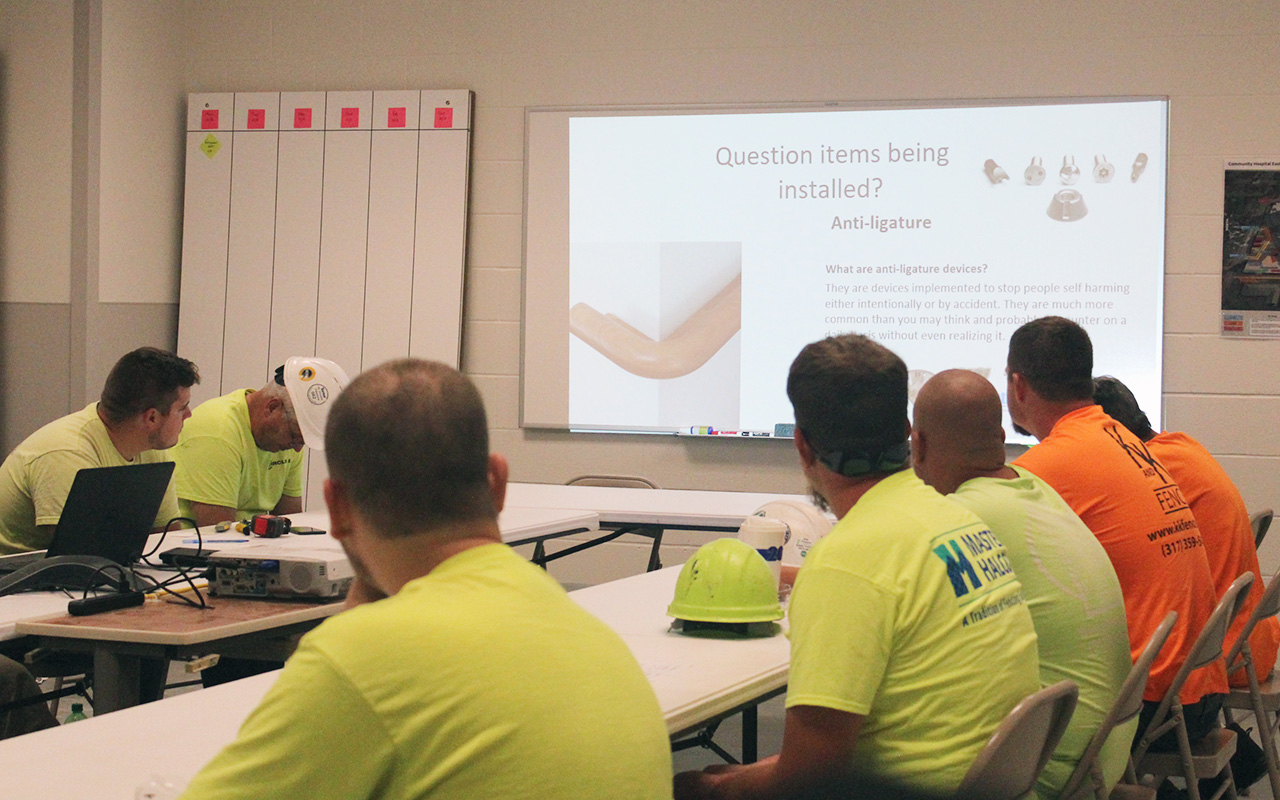
The utilization of our industry's best practices can be approached with a level of empathy that enhances the project teams' ability to meet or exceed these facilities' specific requirements.
As the CM at NDI, Pepper was tasked with guaranteeing 34 state-contracted prime contractors would adhere to the strict requirements and regulations necessary to translate the design into a safe reality. We set out with a goal: create a culture of caring and empathy that makes every trade partner an expert and advocate for achieving the highest level of quality and safety, regardless of their contract or previous experience.
How?
By tapping into people's empathy. Communication and education were key – before the trades even stepped onto the jobsite.
Every tradesperson was required to participate in a project-specific orientation, where they learned about the facility and the risks to patients and staff from improper installation. It was stressed to them that units in certain areas of the building require specific materials; if a tradesperson ran out of a certain type of screw, they couldn't
substitute it with a different type that was just sitting in their pocket. Doing so could result in injury to the future occupants.
To reinforce the message, Pepper provided quality detail visual handbooks and authored bulletins to further inform trades' understanding of risk levels and the importance of material selection in different areas worked. This approach of compassion empowered the tradespeople to alert the project team if something seemed amiss, like questioning if a bullnose piece should be used in place of a straight edge. It prompted more questions and ownership from everyone – all without the contractual obligations.
Renovating behavioral health spaces
Renovating an occupied space can quickly turn hypothetical situations into reality. For example, during renovations of an existing behavioral hospital, workers may think that the precaution of blocking off the construction area with a locked door and temporary walls that extend to the ceiling are enough to protect and separate patients from the work area and tools. However, despite these precautions, patients can be determined and creative in finding ways to climb over the wall – like through a ceiling tile – to get to the other side.
Hopefully, medical staff would stop the patient from completing their plan, but extra precautions should be taken by the team. Locking each room in the construction zone – with the tools inside – ensures that even if a patient manages to climb the temporary wall, they won't have access to materials that could harm themselves or others.
Even though many of the patients may seem docile and nonviolent, you never know what could be a trigger for them. In those situations, the safety of the tradespeople also has to be considered.
On some projects, the trades may come into contact with behavioral health patients. As a precaution, we have everyone work in teams of two so that if needed, one trade can guard tools and materials while the other focuses on the work. If one person has to step away, the work must pause. The priority is keeping everyone safe, even if it takes a little more time and patience.
Using this method trains the trades to be watchful. It's important for everyone working in the construction zone to be vigilant of patients close to where activities take place – even if patient actions don't directly impact renovations. Our teams can offer an extra set of eyes unrelated to our work, like if an electrician sees a patient snag a bottle of shampoo from a housekeeping cart. Even though it could innocent, to wash their hair, it could also be digested by the patient or used in another manner to cause harm to himself or others.
"It's important to take the approach that you cannot put anything past anybody. You have to stay extra vigilant. We're not just looking out for ourselves, we're looking out for the patients and staff, too." – Pepper Superintendent Josh Gearries
Making patient and staff safety the priority
It's true that good communication, understanding the end user, teamwork and quality work is important for any project. But from executives to laborers, heightened engagement is imperative when renovating or constructing a behavioral health facility.
It has to be at the forefront of your mind throughout the entire process that mental health is healthcare, but that it has needs and risks beyond those found in other medical facilities. Keeping the safety of patients and staff – and the atypical challenges in doing that – is a massive responsibility. It requires everyone to take to heart the potential for patients to use the building to hurt themselves, staff and the facility itself.
Compassion goes a long way. And at Pepper, we've learned that if we bring an added level of care throughout the process, we can give patients, staff and their families one less thing to worry about.
About the Author
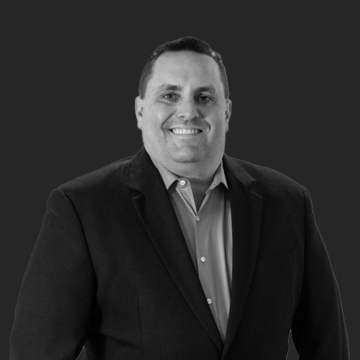