Unlike an automobile assembly line, in construction we rarely build the same building twice. Some say that every building is a prototype. I think of a construction project as a complex puzzle with thousands of pieces that must fit together, be compatible, and meet the design intent.
Project plans and specifications are the design team's instructions for the contractor to complete the puzzle. In a perfect world, this works. Perfect plans, perfect specs, perfect weather, perfect site, perfect subcontractors, perfect materials . . . you get the idea.
Accounting for the imperfect
Unfortunately, no projects are perfect. If they were, the average rate of re-work would be close to zero. Instead, the average rate of re-work -work required to be done more than once during or after construction - in our industry is 5-12 percent per findings published by the Construction Industry Institute (CII) in 2005.
At Pepper, our 2016 rework rate is 0.37 percent and our five year running average is 0.35 percent. We believe our results are different because our approach is different.
Construction is an imperfect process. Not only is it imperfect, but it's fluid - materials, methods, designs and codes are constantly changing. Someone on the project team must have a cutting-edge understanding of the building elements and the best way to piece the puzzle together.
Some contractors take the approach of hiring this understanding using consultants. While consultants play a key role in construction, their focus is often too narrow.
We see this challenge differently. Pepper's quality department seeks to maintain a best-in-class understanding of construction materials, methods, designs and codes and to convey this understanding to our project teams. By keeping this expertise in-house, we are a resource that is always available to assist our teams with anything from a quick question to a detailed design review.
It starts with quality department education & certifications
We started with the US Army Corps of Engineers (USACE) Construction Quality Management (CQM) course and certification, which trains individuals on the USACE construction quality process. While this course is an excellent introduction to construction quality management, it is not intended to make participants technical experts in any given field.
As we’ve attended these national conferences, we’ve become more aware that our approach to quality is different. Typically they are only attended by consultants. At the RCI conference last month, I consistently surprised manufacturers and consultants when they learned that I was not only an RCI member but also a Registered Roof Observer (RRO). RCI is an organization of building consultants, and RRO is one of their professional registrations.
We also attend Air Barrier Association of America (ABAA), Building Enclosure Science Institute's BEST conference, CONSTRUCT, SWRI, Building Envelope Council (BEC), AIA, ALA and others. We are among only a handful of general contractors at these conferences. We also take advantage of manufacturer-led training by Firestone, Carlisle, STO, Dow, Master Builder, CETCO and others to gain an in-depth understanding of what it takes to install materials properly per the manufacturer's instructions.
Corey Zussman, director of quality management in Chicago, has taken education to another level. From RCI, Corey maintains certifications as a Registered Roof Observer (RRO), Registered Exterior Wall Consultant (REWC) and Registered Waterproofing Consultant (RWC). He is truly a best-in-class construction quality professional. His expertise is well sought after, as he has presented at the ABAA national conference and will present this year at the CONSTRUCT conference.
Project impact
The next challenge is taking this wealth of knowledge and distributing it to all of our project teams, where the work is planned and executed. We do this by participating in key project activities along with the team.
Constructability reviews
Pepper's quality professionals conduct a constructability review of the plans and specs. During this review, we leverage our in-depth education and training, along with extensive jobsite experience, to identify potential design issues in material selection, constructability and compatibility. Often this review is complete before the trades bid the work, resulting in better details at a lower cost than if the issues were discovered during construction. The constructability review process raises the education and awareness of our project teams and design professionals.
Building envelope coordination
After the trades are awarded, Pepper leads a building envelope coordination meeting to compile the expertise of all parties, with the goal of reducing field conflicts and warranty claims due to material compatibility, incomplete details and construction sequencing. This meeting is an opportunity for Pepper's quality professionals to educate the subcontractors - and often vice-versa. It results in a shared understanding among all the subcontractors of how the most complicated details will be constructed, and it is a learning experience for everyone present.
Preinstallation meetings
Before a subcontractor starts work, Pepper holds a preinstallation meeting to review the plans, specs, submittals and manufacturer's requirements. We use a series of our own pre-installation lessons learned templates for each trade.
In many cases, the subcontractor is unaware of a specification or manufacturer's requirements and would not have followed them if not reviewed during this meeting. It's not that subcontractors are trying to cut corners; they are just relying on their experience and what has worked on past projects. By conducting this detailed review with each subcontractor, Pepper is educating our subcontractors (again, often vice-versa), and looking out for the best interests of the owner and design team at the same time.
Jobsite reviews
All the efforts to educate our teams and coordinate the work are wasted if it is not translated to the field. To that end, we walk our jobs to verify the project is being constructed per the plans and specs and manufacturer's requirements. We issue consultant style quality review reports, designed and developed by our quality team, that require a photo response from our project teams.
Though non-conformance items are sometimes hard to resolve in the moment, they too are educational. Our project teams and subcontractors are not likely to repeat a mistake once it's been identified and understood. This is raising the education of the tradesmen in the field while looking out for the best interests of the owner during construction.
Quality metrics
Pepper provides a detailed set of quality metrics that is unique in our industry. Our metrics for each non-conformance issue includes estimated cost to repair, including the cost to manage the repair; severity; if the issue was previously discussed; if the issue is a repeat on the project; root cause of the issue and others. These metrics allow our quality department and project teams to identify trends on the project and any subcontractors that may need closer supervision. It makes our program proactive, getting ahead of the issues before they become issues.
Quality assurance
In construction the old saying goes, "good, fast, or cheap – pick two out of three". Typically, the superintendent pushes the job fast and the project manager buys it cheap, but on your construction project, who ensures it's good? I've not yet met an owner who was ok with only two out of the three.
At Pepper, our in-house, best-in-class understanding of construction materials, methods, designs and codes is raising the bar in educating our tradesmen, subcontractors, project teams and design teams, which in turn, improves quality and lowers the amount of re-work.
About the Author
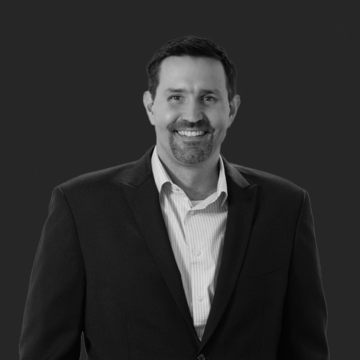