A 24-acre complex adjacent to the Purdue University Airport in West Lafayette, Indiana, attracts the likes of Boeing, General Electric, the National Aeronautics and Space Administration (NASA) and the United States Air Force. Here, at the Maurice J. Zucrow Laboratories in the Purdue Discovery Park District, students, faculty and staff conduct some of the world’s most groundbreaking research in aerodynamics, aeroacoustics, combustion, computational fluid mechanics, particle flow heat transfer and atomization processes.
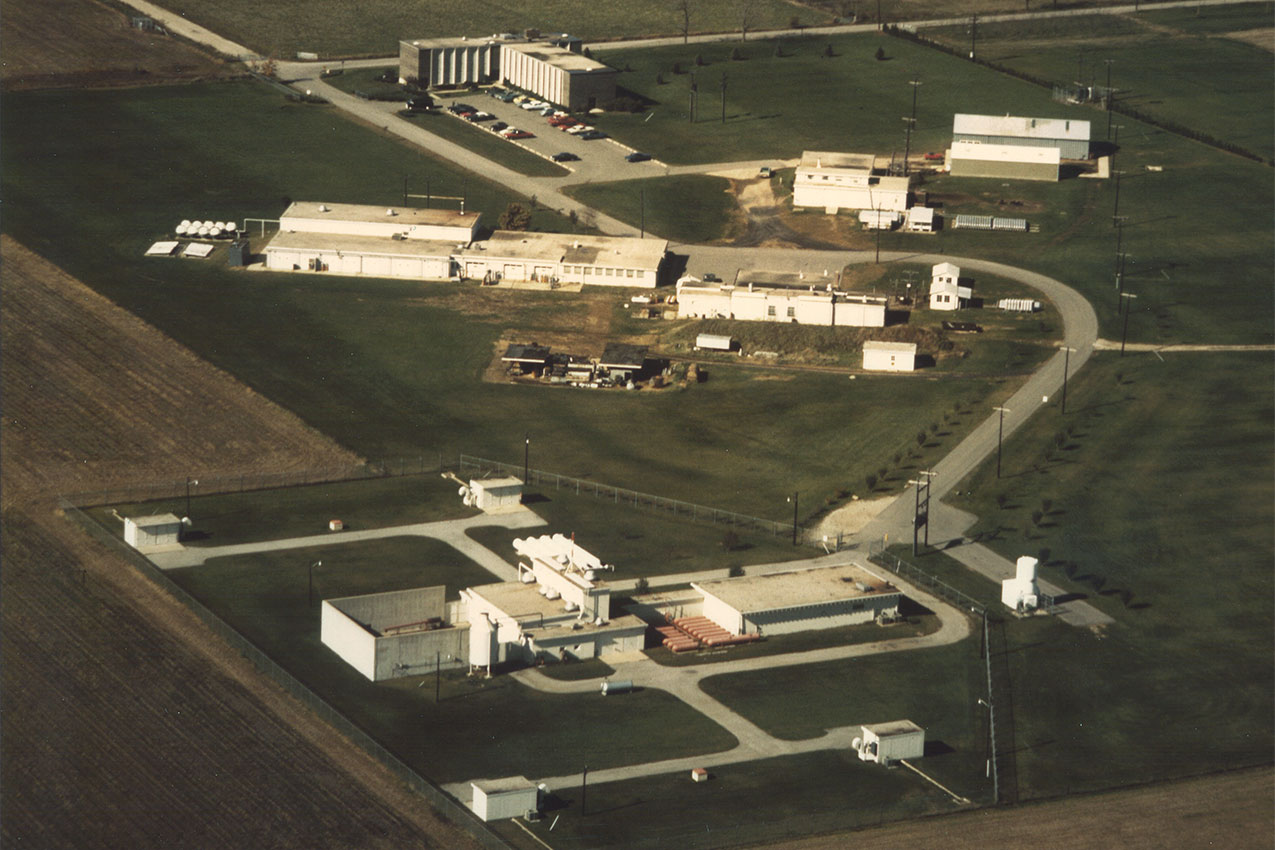
Founded in 1948, Zucrow Laboratories is the largest academic propulsion lab in the world. This hub for hypersonics is named in honor of Dr. Maurice J. Zucrow, who earned Purdue University’s first Ph.D. degree in 1928 and later taught courses on jet propulsion and gas turbines. His groundbreaking research in high-pressure combustion and film cooling contributed to the design of the RS-25 Space Shuttle main engines, still used today after never failing a mission.
Now, with the addition of ZL9, a state-of-the-art high-speed propulsion laboratory, Pepper Construction is helping to advance the Zucrow Laboratories’ nearly 80-year history of research and development in rocket combustion and gas turbine engines – beyond levels already unrivaled in academia. Covering approximately 54,500 square feet, ZL9 features leading-edge capabilities that put the university’s hypersonic testing on a scale with government and industry partners.
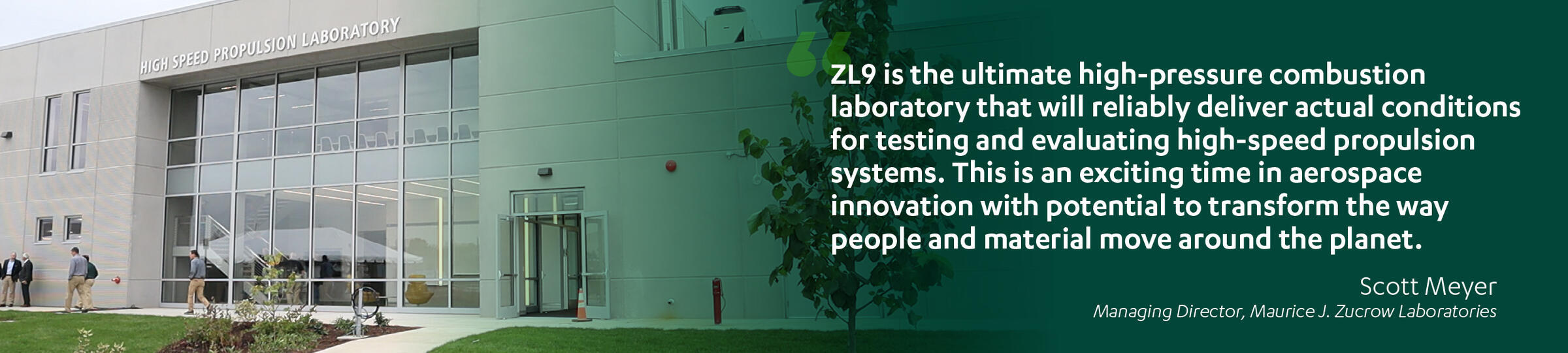
Testing under hypersonic flight conditions
The lab includes substantial infrastructure that creates the extreme pressure and temperature conditions experienced in actual hypersonic flight – the ability to propel flight systems to Mach 5 and further. The facility adds five new test cells that are 30 feet by 55 feet with 12-inch-thick floors and 18-inch-thick walls of cast-in-place concrete. Each cell has a dedicated climate-controlled laser diagnostic facility, control room, workshop assembly space and machine shop. Specialized hot-air piping delivers air at 1,500 degrees Fahrenheit and 800 psi, and a new compressed air plant supplies researchers with 3,400 psi air at 5 lbm/second. Liquid jet fuel tanks and high-pressure gaseous propellants along with specialized instrumentation round-out the facility infrastructure. The extreme energy being produced and released in the test cells required an elevated attention to safety in the design of the facility, including ballistic-rated doors.
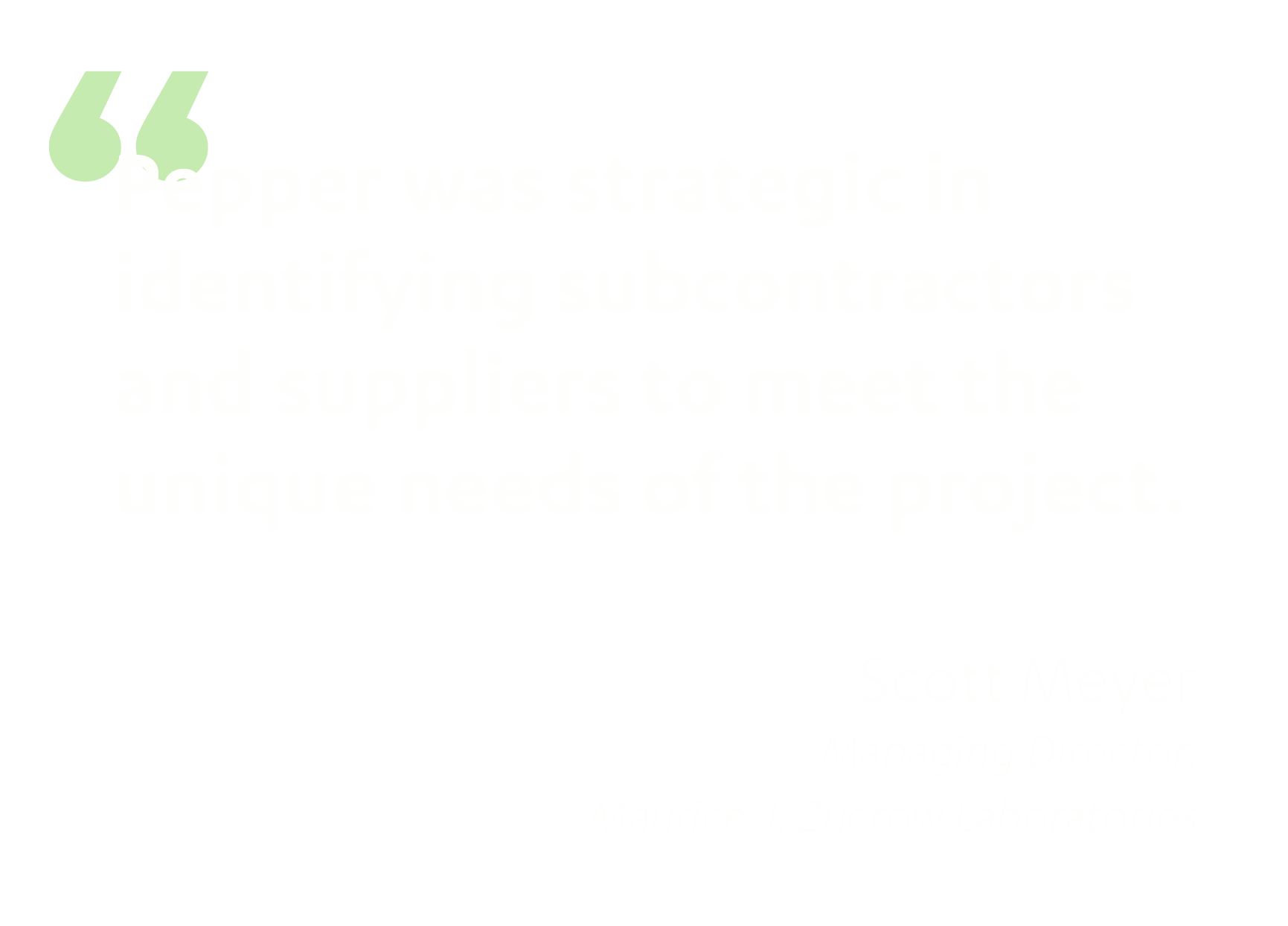
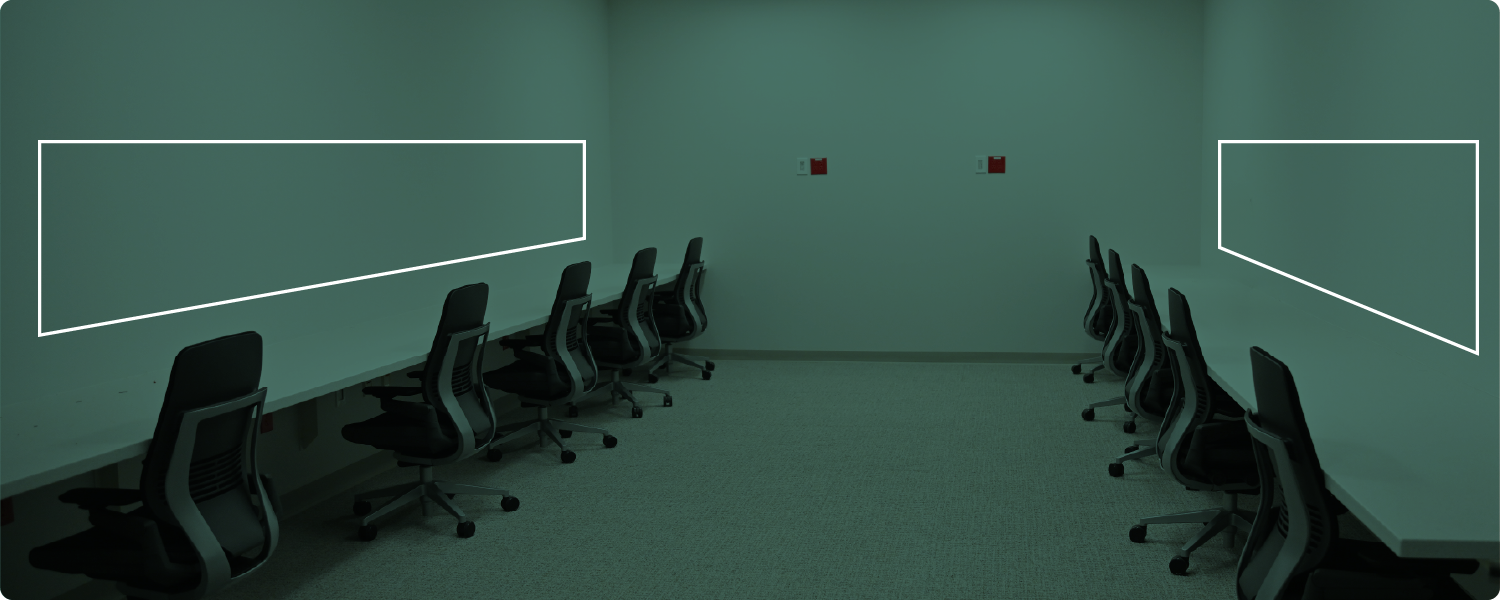
The control room will include mounted computers on the walls and consists of noise reduced insulation that will protect the researchers from the testing cells vibrations and noise levels.
With coordination in mind, the team implemented extensive Building Information Modeling (BIM) for mechanical, engineering and plumbing (MEP) underground and above-ground utilities. “The project was designed to have almost 800 rammed aggregate piers for soil stabilization, which required detailed coordination between the piers and the underground MEP, including more than 1,000 feet of underground electrical duct banks,” says Pepper Project Manager Clayton St. Martin.
Utilizing a GPS unit to capture as-built data on all underground utilities, the team effectively marked the utility locations on the surface after completing the backfill. This eliminated guesswork for subsequent trades, which could have led to costly delays, last-minute changes and rework.
The interior buildout of each test cell also needed to cater to specific testing needs. Conducting BIM reviews in an auditorium and integrating virtual reality in smaller breakout sessions enabled the team to share updated information with key stakeholders to visualize the space and identify potential issues early.
Elevating and expanding the workspace
Pepper’s expert navigation of the complex “what-ifs” in constructing ZL9 means world-class researchers will have leading-edge capabilities in hypersonic exploration – a not-so-small step that propels a giant leap forward for the future of flight.
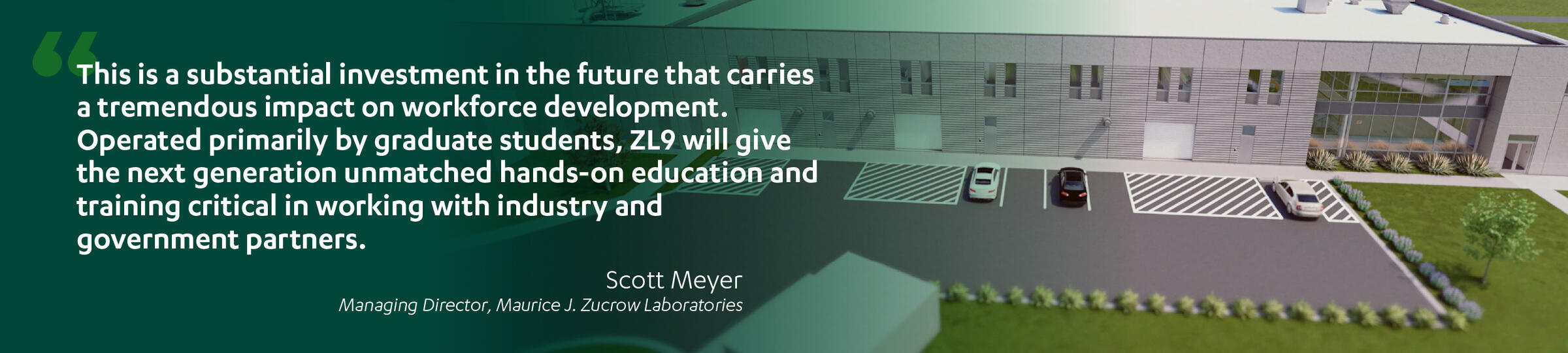
Credits