Quality, Science + Technology
Inventions are exciting and make our lives better, and our industry is full of new ideas. At Pepper, we like working with creative and imaginative architects who dream up unique designs. Often, it's their way of putting their own stamp on the design, but they're also good problem-solvers when it comes to challenging design issues.
While our trade partners are experts in their craft, as the contractor, our role is to ensure the design works – that all the parts and pieces come together correctly to fulfill the owner's vision. From our experience, we apply the math and science of construction to make structures strong, buildings weathertight and ensure materials last for the expected life of the building. So, what happens when faced with a unique design element or a product or system we've never installed – whether brand new or new to us? That's where our Quality Management program becomes critical in achieving a successful outcome.
I recently returned from Arkansas where one of our ACIG partners gave a presentation to our Quality Peer Group on understanding and managing risks. They are constructing the largest timber frame structure in the United States at the University of Arkansas, which is certainly a novel approach to building. The design includes columns, beams and decks made of wood, which we were told is more sustainable than traditional construction with steel and concrete. It was fascinating to hear their approach to the challenges of installing a new application of an old building material. They leveraged their relationships with the manufacturers and trade partners, as we have when faced with similar situations.
Process for managing quality of new installations
When we encounter something for the first time, we start by understanding the product or system, and depending on what it is, we take different steps to evaluate it. Questions we try to answer include:
- What is the benefit to the owner?
- What are its strengths?
- What are the risks? What could possibly go wrong?
- Are the installers qualified and know what they're doing?
- How will we check for quality? What are the inspection points and tolerance metrics?
- Who measures and determines success - third party, engineer or trade partner?
We just completed installation of a Cobiax structural system on a medical office building addition at Schneck Medical Center in Seymour, Indiana. The system was specified by the engineer, Lynch Harrison Brumleve because of its flexibility and lighter weight to match the low floor-to-floor heights of the existing building. The Cobiax system is a different, more eco-friendly approach that uses recycled materials instead of metal slabs. It's considered a voided slab system, and though voided slabs have been around for a while, the Cobiax system is relatively new. While more common throughout Europe, there are only 10 buildings that have used the system in the United States.
"To minimize the structural depth of the new construction, a cast-in-place concrete flat-plate system was selected. Using a voided slab provided additional benefits in that it reduced the overall volume of concrete required, further minimizing the thickness of the slab required. In addition, foundation sizes were reduced significantly by eliminating additional dead load from multiple floors."
Scott Clore, P.E.
Principal, Lynch, Harrison & Brumleve, Inc.
Becoming one of the experts
We have been working with the team through the entire quality management process. New systems introduce new risks in new ways so we started early to plan for calculated and informed decisions that would mitigate our risks. For us to be successful, we needed to have the same level of expertise – or more - as our trade partner installing the work.
A detailed process was followed to make our entire Pepper team, as well as our partners, aware of the risks and opportunities.
01. Meeting with the trade partner - Even before meeting with the architect and engineer, Pepper sat down with the structural contractor, Wilhelm, to learn from them. They had already done some research about where the Cobiax system had been used in the United States and how to install it.
02. Reviewing plans and specifications - Our team then poured over the cross-section details and read the specifications - reviewing where it's installed, looking at the profile and slab thickness and rebar installations. Had the mechanical, electrical and plumbing (MEP) systems been designed, we would have also reviewed the drawings for conflicts.
Critical details were incorporated into our Job Specific Quality Plan (JSQP) for heightened attention by the entire team.
03. Touring a project under construction - In this case, we were fortunate that one other Cobiax system was under construction, a small group flew to Washington DC to observe the installation on the John F. Kennedy Center for Performing Arts. We made the trip just in time, as the process was nearing the end. We saw the last slab pour. The tour turned out to be a critical step in our quality management process.
We conducted a Gemba walk of the project and were as thorough as possible. A Gemba walk is a concept from Lean Construction and describes personal observations of work where the work is happening. (Learn more about Gemba walks.)
Conversations and observations included the following:
- Interviewing the site quality manager, site superintendent, foreman, laborers and even the pump truck operator – to get a feel of the system from all perspectives. We talked about defective installations, accessibility, process, etc.
- Examining the products on site. It was helpful to see the defective products on site and understand what made them defective.
- Reviewing specific operations and installation processes and learning what worked and what didn't. We also took notes for how to mediate an issue if something went wrong.
- Monitoring during installation and how to quantify defective spheres that remained in the slab.
We were appreciative of the opportunity to learn from the current project in Washington DC – that the team was so open and forthcoming - because as we dove into the reasons why and the nuances between the manufacturing specifications and the practicality of implementing them in the field, we understood how and when the process might differ on our own project. We also learned how to be prepared for failures in the process, which saved some of our own pours. In fact, we had no re-work, which we attribute to the Gemba walk.
04. Attending specialized training - The final step in becoming an expert was attending training. While the training didn't specialize in the Cobiax system, we took the opportunity to sit with like-minded people to discuss voided slabs potential issues, problem-solving, and suitable mix designs. One suggestion was to get the manufacturer's representative on site with the structural engineer to observe the process.
05. Holding a preinstallation meeting - As the construction manager, it would be easy to rely on our trade partner to get the job done – and often that's what happens. However, at Pepper we apply a more comprehensive approach to quality, where once armed with the knowledge of how the work should be installed, we then get the entire team together - Pepper, engineer, trade partner and supplier - to discuss the process in a pre-installation meeting. It's a checks and balances process that is part of our quality management program on all projects, and it serves as our last line of defense.
In the preinstallation meeting we discussed our observations on the site tour and some of the defects we saw. We strategized about the differences in our environment (e.g., traffic and weather) versus the east-coast and how that could impact our installation. We agreed to similar measures that worked for the project in New York, as well as new measures for mitigating the different risks to which we could be exposed. Finally, we established an installation sequence and guidelines for each pour.
Because we toured the project as a team, the pre-installation meeting was an educated conversation. We all saw first-hand the challenges instead of speculating, which put us on the same page and allowed us to form a common front.
06. Monitoring for quality - Another critical role that the construction manager fills with new installations is quality assurance during installation, and we could not have done that without first understanding the Cobiax system.
The Cobiax system allows for a tolerance of defective spheres, which are either filled with concrete or replaced when defective. Since the viability of the structure is based on weight, our team was careful to document every defective sphere in each pour. Without the data on how many were broken and filled with concrete the entire structure could be at risk, and the engineer would have no way of knowing.
Finally, we partnered with an independent testing agency and conducted pre-, mid- and post pour inspections.
Applying knowledge across all trades
Another aspect that was closely documented was the MEP installation. The structural engineer doesn’t take into account MEP systems, and even though the MEP designs weren't completed and purchased until the fifth-floor pour, we still had to coordinate for them. Using our in-house Virtual Construction Department, we installed sleeves and hangers based on early designs and where we thought they would be needed. With a Cobiax system, it was critical because though we can core into the Cobiax system, the strength of the slab is in the steel rebar, which can't be touched. Our goal was to minimize the need to go back, and just in case, our team marked areas as we went that would be safe to core later.
Creativity initiates more creativity
We have found the design firms that specify new systems will also try new products and applications, as is the case on the Schneck MOB project.
Last week, we held a pre-installation meeting for using spray foam as the exterior installation. The architect, arcDesign, specified the application because spray foam provides a seamless installation better for continuous insulation. A handful of projects in Indiana have used this application, but it's the first time for us to use spray foam at the exterior.
One concern was that with building movement over time, the spray foam has the potential to crack. If we are using the product as the all-in-one air barrier and thermal barrier, a crack could potentially allow air infiltration through the sheathing joints behind the spray foam. We reviewed this concern with the design team and recommended that we seal the sheathing joints prior to applying the spray foam to provide a backup air barrier in case the spray foam should crack. Our plan is to build mockups to test the solution and how it performs.
And of course, the spray foam installation requires a new product – Flash Trac - a special masonry flashing which is installed prior to spray foam. We discovered this product while reviewing our installation sequencing concerns with the spray foam trade partner during a preconstruction design review. The Architect agreed to specify the product, and we reviewed it during the preinstallation meeting for both the mason and the spray foam trade partners.
And finally, a word of caution
When planning for a new installation, it's easy to get distracted by the shiny object and loosen your oversight on other parts of the project that should go as planned. It's important to be mindful that you're not the only one who is concentrating your efforts and putting your top resources toward the new installation. If your trade partner is involved in other aspects of the project, it is likely their focus is also on the unfamiliar installation. As the construction manager, it's our job to ensure the entire project is constructed as designed.
Partnerships make the difference
If you're looking to install a new system, it's important to get the right partners on board who have the right experience and bent toward collaboration, from the architect and engineer, to the construction manager and trades. You should be asking what kind of Quality Management program your construction partner has in place and the measures they plan to take to assure the quality you expect.
About the Author
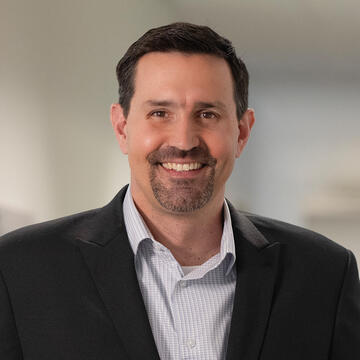