Quality
Improving quality through a cultural transformation
Pepper's name has always been synonymous with quality. Even before we had a formal program in place, we cared about doing good work and made it a priority to take care of our customers. In Indiana, our current quality program is 10 years old this year. It emphasizes continuous improvement, and it's certainly seen its successes and failures. Almost immediately, we saw our warranty costs drastically reduced when we started our current program.
Today, we generally believe our program to be among the best in our industry. So, what made our quality program effective, and how do we take a good program to the next level?
Designing a program that encourages innovation
Anyone can download a quality program from the internet, make a binder and BAM - instant quality program! It would likely include a nice library of checklists and a series of steps to follow in the construction process. The thought goes: follow these steps and checklists, and the work will be installed correctly. In my experience, that is not the case.
Checklists and processes have their place without a doubt, and ours includes this kind of foundational structure. But unlike manufacturing, in construction we build a different product every time, with a different design team and a changing mix of trade partners. Add to that ever-evolving construction products and technology, which are all designed to allow work to be installed faster, cheaper and in worse weather conditions. We needed something that was flexible for different variables and that encouraged our people to adapt as well.
Our quality program has all the right components to set up our project teams and trade partners for success on a job. It includes both project management and field supervision, as well as our integrated construction services group (in-house quality team, preconstruction, virtual construction and MEP, and safety). Our program actively engages the owner, design team and trade partners. It starts during the estimating process and extends beyond close-out.
But guidelines and rules don't always look for the best way. To encourage our people to explore new ideas and evolve our program, we also include forums that encourage sharing ideas, like ongoing training, access to the latest technology and our Quality Concept of the Year recognition program that shares both successes and failures. Often the ideas shared are innovative solutions and evaluations of new products and processes that are explored.
Why a quality culture is important
Despite our success, we've found that having a quality program is quite different from building a quality culture because it's not our program that builds a quality product for our owners – it's our people.
People make small individual decisions, which add up to a good, bad or mediocre construction project. Everyone plays a role in building a quality culture - from the tradesperson with a hammer on the jobsite, to the project manager writing contracts, to the coordinator in the office assembling submittals. Recognizing that our people and their decisions have a significant impact on our work product, we realized that changing our mindset was required to take our program to the next level.
Finding out where we really stand
We started by asking our own people and the tradespeople on our jobsites about our quality culture. People were asked whether they believed quality was more important than cost and schedule, if they knew their quality responsibilities, if they felt empowered to stop the work if they saw an issue, if they believed that all defects were preventable, and more. ACIG, our insurance group, partnered with us by administering the survey and summarizing the results as a third party.
Digging deeper by asking questions about what motivates behavior revealed room for improvement. We found that we do have a quality culture, and it's okay. Not outstanding and not bad. Just okay. Our teams feel quality is important . . . most of the time. They felt somewhat empowered to stop the work, and somewhat agreed that all defects are preventable. To some, having a culture of quality would be encouraging. But for us, we learned we aren't where we want to be. We aren't satisfied with being okay. We want to be the best.
Our next step was to bring everyone in to discuss the results and talk about the way ahead. We presented our 10-year path of quality and asked if everyone was satisfied. Were we pleased to be the best in Indiana? Or could we still improve? We challenged our people to think about their commitment to quality, and we asked each person to engage as leaders for quality on their projects.
A fresh approach
Our vision of a quality culture is when Empowered project teams and trade partners take ownership of the work and build it right the first time.
In the next few months, we will be holding Quality Management 101 courses to teach our teams the technical skills to be ambassadors for quality on their projects. Equipping them with the right construction knowledge will empower them to assure quality on our projects and raise the bar of expectations for our trade partner community. We will also be providing more accessible information and tools, through our quality bulletins and Pepper app, and sharing additional information about our performance so our teams can take ownership of the results. By doing this – shifting the focus from compliance to commitment – we believe our people will take our program to the next level.
In the near future we will be engaging our trade partners as well. We want them to join us in this challenge to improve the quality of construction for our industry. As John Kennedy famously said, "A rising tide lifts all boats," we hope to be the tide of change and lift the level of quality construction for everyone.
About the Author
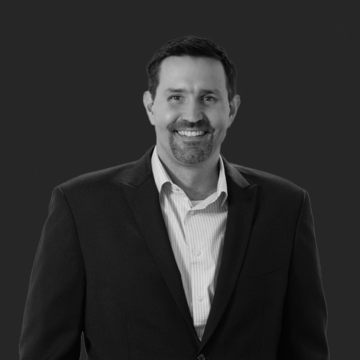