Virtual construction & technology, Safety, Trade partnerships
When it comes to hitting an underground utility, the list of potential negative consequences is long: property damage, interruption of critical services and even serious injuries or fatalities. Our greatest responsibility as a contractor is to ensure the safety and well-being of our tradespeople, our clients and their customers, as well as the general public. And we must take that responsibility seriously.
Pepper has always had above standard processes in place to help us avoid hitting underground utilities, and while our results had improved over the years, we were still seeing utility hits on our jobsites.
We recognized it was time to start digging in and see where progress could be made.
It was clear that for us to get serious, we would need to bring our trade partners into the discussion. We opened a dialogue with a group of trade partners who regularly perform underground work on our projects. During the brainstorming session, we wanted to identify our biggest challenges, where processes were breaking down and, ultimately, why we were still hitting utilities on our jobsites.
Collaborating with our trade partners to find a solution
The group of trade partners we brought together included firms that are used to competing against one another for work. We asked them to be open and honest about what the issues are and share their experiences for the common good. It would have been easy for them to hold back and not divulge too much information, but it quickly became apparent that they were just as frustrated with the way this process works in our industry as we were! We walked away from our initial meeting with several takeaways and observations about what the issues were, but they can probably all be summed up in three categories:
- Poor communication
- Lack of process consistency
- Culture of complacency
So why is this even an issue in the first place? Why do we hit underground utilities?
As our Safety Director Dave Murphy stated in our first meeting, "Because you can't see them!"
It seems like such a simple observation, but it's actually the heart of the issue. If we could see the utilities, wouldn't we be less likely to hit them? Even after calling 811 and researching underground line locations, drawings and information provided are incomplete, inaccurate, outdated or nonexistent. Diggers can't see where the lines lie, resulting in utility strikes, despite taking the proper steps.
Those gaps of information make it difficult to have a consistent and thorough process in place and create communication issues. It left us wondering if there was anything we could ever do to find hidden lines in advance.
We began to explore the potential of using BIM and 3D modeling to help fill this void. We put together visuals all the time, but we had not yet seriously considered BIM as an avenue to help us improve digging underground.
"We walked away from our initial meeting with several takeaways and observations about what the issues were, but they can probably all be summed up in three categories: poor communication, lack of process consistency and culture of complacency."
When discussing this with the group, everyone agreed that there was potential benefit. However, several concerns were raised: how much it would cost? How will the most accurate and relevant data be collected? Do all trade partners have the capability to utilize the technology? What impact does this process have on a project schedule?
These were all similar concerns that we heard years ago from our MEP trade partners when it came to using BIM for 3D MEP coordination. Fast forward to today and using BIM for MEP coordination is standard practice in our industry.
With these considerations in mind, the Pepper team went to work outlining what this new underground utility process could look like. From start to finish, we outlined the steps that would need to happen, who needed to be involved and the ideal timing for each step in the process.
Mapping the process
Our underground utility process already included gathering all site utility as-built information, performing public and private utility locates and performing potholing, but we added an additional seven steps into our prevention process: an underground utility kick-off meeting; incorporating milestones into the master schedule; surveying utilities exposed during potholing; capturing an aerial photo; developing, coordinating and distributing a 3D model and visuals to the field and maintaining the as-built model for turnover to the client.
The new process focuses on capturing highly-accurate information at the right time during the project, which typically means the earlier the better. We want to get eyes on the utility by potholing the utility. Next, using a total station, we capture and document the location, elevation, size and type of utility. We then take that survey information and build a 3D model of all captured utilities.
There are other methods for capturing and documenting the data but none of them are as accurate as capturing the data on an exposed utility that you can see. We then overlay that model with the new utilities and other building elements that are below ground and review for coordination. Finally, we deliver an as-built model to our clients at the end of the project for future documentation and use.
Testing our ideas
After this initial process was developed, we met with our group of trade partners again to share our preliminary approach and gain their feedback. We asked for honesty, and we were honest ourselves. We outlined the limitations of the process and reiterated that the process would only be as good as the effort and commitment that a team puts into it. Just introducing a new process won't completely eliminate the risk of an underground utility hit. However, if implemented properly with buy-in from all involved, it's a process that could significantly reduce everyone's risk and change the way our industry performs this type of work.
Since that first roundtable, we have used Pepper's new underground utility damage prevention process on five projects, and we can already see the difference. We hold lessons-learned meetings with our trade partners and project teams upon completion to evaluate how it went and continue to evolve this new process. We have big ideas for the future, and we are excited about the direction we are headed. The open and honest engagement of our trade partners was critical in helping us develop this process and will be essential to its continued success.
If you would like to learn more about our virtual construction services and how we can help you, please contact us.
About the Author
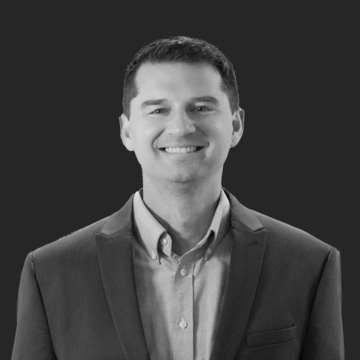