Safety, Emerging technology, Virtual construction & technology
About 15 years ago we changed the way we look at safety on our jobsites, from measuring events after they happened to measuring predictive indicators - the environment and situations that encourage negative behaviors. The goal was to take corrective action before a safety event would occur. Through this approach, we saw the number and severity of safety incidents on our projects decline. Others in our industry took note and followed our example.
We could not have made this switch without incorporating technology into the solution. At the same time that we shifted our mindset, we transitioned our audit process from paper to electronic format. Not only was it more efficient, it opened the door to a new world of data and the ability to identify trends - and share them more broadly with those in the field in a timely manner.
Sadly, our industry still has a ways to go, with construction claiming 20% of work related fatalities. Our goal is to eliminate these incidents, and that's why we continue to seek out emerging technologies as a means to creating safer environments for our workforce.
At Pepper, we've seen and tested several new concepts that help move the needle. Though the benefits are worth exploring, it will be a while before their impact will be felt across all our jobsites.
- Prefabrication places activities in a safer environment. But the reality is that construction still requires on-site work. And prefabrication is not the practical or financially beneficial answer for every job.
- There continues to be a buzz around wearables, but to really impact our safety stats, it has to be affordable and available to the masses. It will be a while before we'll be wearing smart helmets.
- Safety apps make information readily accessible and provide real-time alerts. We use one at Pepper. But its use tends to be more reactive than preventative.
As the industry finds ways to apply the above solutions more broadly, BIM has made two innovative construction safety products available to all our jobsites, which means they have the biggest potential to impact safety today. We consider them game changers.
Virtual Reality safety training - Our workforce tends to be visual, hands-on learners, but traditional training is largely based on a classroom type atmosphere. The two styles don’t match and often result in a learning gap. So we researched what we thought was the future of safety training: virtual reality. A virtual environment is the closest we can come to physically being on a jobsite while also addressing our most common safety hazards.
At the beginning of our search, we didn’t find a specific solution that met our needs. Commercially-available options were either not cost effective or too generic. Instead, we tapped our own in-house expertise to build a training program. The process was straight-forward and based on our own safety data:
- We decided to limit the focus of the training to a single scope of work to make it specific enough to be effective. We chose our vertical concrete operation.
- Then, we analyzed previous incident and hazard data and developed the content of the training to address the most frequent safety exposures on our jobsites.
- Our Technical Services/BIM team worked closely with our field supervisors to make the concept relevant to our teams.
- The images were created from 3D scans of our concrete crew work spaces to make the graphics realistic and recognizable.
The new training is shown to new tradespeople to communicate the conditions and hazards they will experience shortly after safety orientation. So when they arrive on site, it’s almost like they have been there before. The VR module allows for increased interaction between our safety representative and our new tradespeople.
Underground Utilities Damage Prevention program - Our Underground Utility Damage Prevention program combines field operations with 3D modeling. In the past, we located utilities and would mark them on the surface or insert sight tubes so the locations of the utilities would remain throughout the project. However, there remained too many unknown variables, which left room for human error. With our UUDP plan, we are able to create a 3D model of all underground utilities on the jobsite before machine digging. This deliverable is then provided to each contractor in advance of their on-site operations. An underground model also allows us to add as-built information and turn over a current and accurate deliverable to the client that they can use on all future projects.
What's next with safety?
At Pepper, we believe AI offers the next breakthrough technology and are actively exploring opportunities to use it for safety purposes. We are very close to applying it on some of our projects in a very practical and effective way. Stay tuned to learn more.
Until we are able to completely remove the dangers from our jobsites, technology will play a critical role in progressing our industry toward zero incidents. But the decision to be safe is still a personal one. That's why as we evaluate a program's effectiveness, it's important that the safety tools and measures we use apply to each person on our projects.
About the Authors
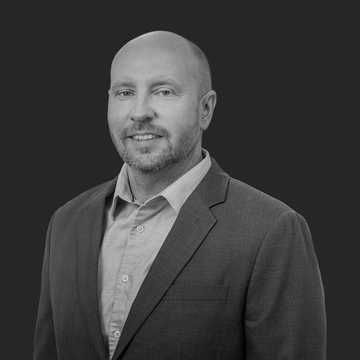
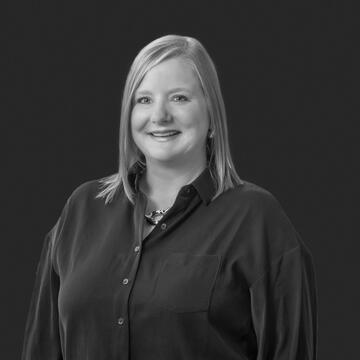