Safety
The importance of daily safety planning
In a city like Chicago, construction is part of the familiar sights and sounds. Barricades close off lanes and pedestrians pass through covered walkways. Jackhammers, saws and the noise from the crew create a distinct kind of rhythm. It's disruptive and exciting at the same time, and it's the norm.
The crews themselves develop a routine as well. They show up, grab their protective gear, check in and get to work. Predictability is a good thing, but in the midst of these routines we tend to let down our guard and coast.
It's like driving a car. Have you ever driven to work and then wondered how you got there? You get in the car, turn on the radio and "autopilot" kicks in. It's a scary thought to wonder what could have happened as your mind escaped and your body continued through the motions.
Construction is full of high-risk activities. MILA is a good example, where our people worked 41 stories above street-level. Height was just one risk. Factor in wind and weather conditions, noise, vibrations and equipment… the hazards quickly add up. Yet, for the crew, each day is the same. They do the same work, just one story higher - exactly as the project was planned.
Repetitive activities are good for productivity and great for lean construction. However, if not carefully managed, repetitive work also breeds boredom and complacency toward safety – allowing the team to stop thinking about what they’re doing. So how do we take advantage of the efficiencies that routines offer without putting ourselves on autopilot?
The value of daily pre-task planning
At Pepper, we implement daily Task Hazard Analyses (THAs) as a standard and best practice. Occupational Safety and Health Administration (OSHA) uses the term Job Hazard Analysis and defines it as, "a technique that focuses on job tasks as a way to identify hazards before they occur. It focuses on the relationship between the worker, the task, the tools, and the work environment. Ideally, after you identify uncontrolled hazards, you will take steps to eliminate or reduce them to an acceptable risk level."
The reality is that every day, every job, every project and every task has something different about it. Completing THAs raises the group's awareness as to what each person is doing, where they are and who is around them. It helps them see how their work affects each other and teaches them to look for and recognize hazards.
THAs provide many benefits, the most important of which is the reduction in the number of incidents and injuries. They also prevent lost time, to workers and in the schedule. THAs help improve the quality of work and increase productivity. Attitudes and morale on the jobsite are noticeably better when all of these items come together, as a result of THAs being performed.
As explained in last week's article about Starting with how we learn, THAs are effective because they are presented in the field and are relevant to the work taking place. They're timely.
Why should safety matter to owners?
The construction industry is considered high risk because of safety and health related exposures. The costs of a single incident can include medical related expenses, employee-replacement costs, OSHA citations, increased insurance, downtime, negative public exposure, damaged product and equipment. As such, safety performance is a factor in the contractor's financial strength, which gets passed on to the owner through competitive rates.
Beyond the initial fees, we see a direct link between safety, quality and productivity – and the overall performance on the project. The measures that are in place to control these factors speak to the strength of a company's risk management program.
Further, we believe that the jobsite safety mindset is influenced at the top, with the owner. At Pepper, we see a correlation between safety performance and owners who make safety a priority on their projects. Generally, the more engaged they are, the better the results.
What do the most effective owners do?
- Actively participate in jobsite walks.
- Wear the appropriate jobsite gear when onsite.
- Provide clear communication with advanced notice of project tours.
- Coordinate any direct-hire contractors with the construction manager so they know who is on-site.
- Coordinate owner-purchased material and equipment deliveries with the construction management team.
- Get involved in the safety tradesperson recognition program.
- Respond to questions and requests in a timely manner, particularly when there is an event.
Best practices for implementing a Task Hazard Analysis
With repetitive work, it's easy for the project team to grow complacent and copy the THA from the day before. Since THAs are designed to protect everyone on site, the following tips help ensure daily THAs are effective and relevant.
- Each trade person should participate in the completion of e a THA. THAs work most effectively with input and involvement from the entire crew. Each person has a unique experience from which everyone can learn.
- They should be used as a baseline from which the crew adds different and non-routine tasks and the hazards or dangers associated with each.
- THAs should be used to share observations, techniques or questions.
- They can be used to communicate weather conditions, non-routine task awareness and non incident project reviews.
- THAs can be used for training a new tradesperson and for refresher training.
- They must never be pencil whipped or used in a sign-and-go scenario.
- Start thinking about tomorrow’s THA, today.
THAs should be designed to start a discussion and ask questions. Where will the electricians be working today? What is the overhead work and the equipment in the area? What are the safety precautions for scissors lifts, inclines, drive-off hazards and hole covers? What if the fire alarm goes off? Remind tradespeople of the importance of stretching and flexing before lifting or carrying materials; inspecting their cords, tools and equipment or looking for signs of dehydration in the severe heat – in themselves and those around them. And don't forget - What can we learn from today to improve tomorrow?
Call to action
One incident is too many. And yet, according to OSHA, in 2014, 20.5 percent of private industry worker fatalities were in construction. The US Bureau of Labor Statistics (LBS) reports four leading causes: falls, electrocutions, struck by object and caught-in/between. According to LBS, eliminating these causes would save 545 lives each year. The need for safety on our jobsites is greater than ever. If we want to change this upward trend, it will take increased awareness and commitment at all levels, every day.
At Pepper, we believe safety is not proprietary. If you have questions or ideas about jobsite safety, let’s talk.
About the Author
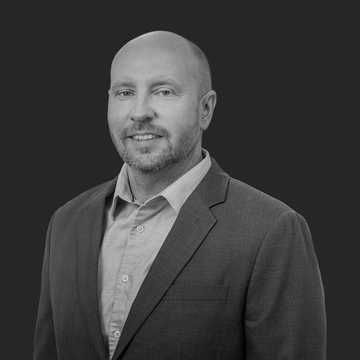