Safety, Quality, High performance & sustainability, Environmental, Self perform, Virtual construction & technology, Industry insights, Trade partnerships
Our New Year’s resolutions for our industry
Skeptics challenge the efficacy of making New Year’s resolutions. The argument is that they don’t work anyway. Particularly when diet and exercise are involved, eventually the motivation fizzles and we return to our former ways. But at Pepper, we believe in continuous improvement. As we enter our 90th year of business, we’re looking toward the future and asking ourselves, “What if?” and, “What’s next?” So in the spirit of excellence, I asked each of our services leaders how they would challenge our industry to progress over the coming year. As we’re honest with ourselves, we hope to inspire others to move the needle as well.
Safety
Our safety leaders work closely together, and though their goals are the same, each talked about them in different ways.
For several years now, Dave Murphy has talked about how safety is not about statistics but about people and the choices they make. Though we’ve made significant improvements in many ways, we’re still not where we need to be. “I would like to see the construction industry continue to move in the direction of tradesmen based safety,” he shared. “For too long, safety has been about rules and adversarial relationships with the people that enforce those rules.”
Likewise, Dan Ruane would like to see improvements made with how the safety plan is developed and implemented with the project team: “Too often our industry puts safety into a silo. We treat the site safety plan as a separate planning session when it should be integrated into all project planning activities.”
At Pepper, we’re hoping to lead by example, as we share how we’re using a more integrated approach between our services and our project teams, resulting in safer, more efficient and higher quality solutions on our projects.
Quality
Our quality team responded similarly to our safety leadership in that they see room for improvement by both project teams and the trades.
Since Heather Siemers also oversees Indiana’s lean program, the very idea of continuous improvement resonated with her. “We’re only as good as the individuals working on our projects so we need them to take ownership in the quality of their work – both personally and as a whole. We need to be challenging them to step up, while at the same time listening to their suggestions, in order for our jobsites to become more efficient without cutting corners.”
She clarified that collaboration isn’t exclusive to field staff. “Not just the general contractor and trades but the owner and design team need to be involved as well.”
Corey Zussman suggests one way to accomplish this is through better communication and planning of the details: “I would like to see pre-installation meetings happen that include other trades before beginning the scope of work,” commented Corey. “Product requirements, cure times, weather restrictions, compatibility, and proper surface preparation are common areas of concern and should all be reviewed and properly incorporated into the schedule.”
“I’d like to see our trade partners take an active role in managing their quality,” shares Ben Dykstra. “Rather than waiting to see what the general contractor will catch or if the work will pass, they are diligently checking their own work, making corrections and advising us on best practices in their field.”
He elaborated further, “Along the same lines, I would like to see project teams working alongside trade partners to check the first work in place to verify that the materials and installation match the project plans and specifications, manufacturer’s instructions and industry standards.”
Utilizing a collaborative, checks and balances approach, we will improve the construction knowledge base of our teams, see shorter punchlists and turn over a better finished product for our owners.
Preconstruction and estimating
This next topic is a big one for our owners – budgeting, estimating and target value design. Our preconstruction team was on the same page in their responses to what will drive us to better numbers – technology.
“With more and more projects utilizing BIM, we are finding new and creative ways to apply this information in the preconstruction world,” explains Brandon Moore. He shared the benefits this brings to a project, from real-time budget updates, to energy modeling and lifecycle cost analysis.
“This technology will enable us to get the proper information into the owner’s hands in a timely manner to help expedite the decision process of changes and value analysis possibilities.”
Paul Riehle shared why he would like to increase collaboration with virtual construction during conceptual estimating. “It allows quantities to be derived directly from the model, and it also provides a visual or graphical representation of what our estimate represents.”
Like Brandon, Paul sees additional benefits in analyzing total cost of ownership: “When we model conceptual projects, we can work with our high performance and sustainability team to provide cost analysis, operating costs of the various mechanical systems and the overall performance of the building, which helps clients better understand how the decisions they make about the initial costs of their building affect their annual operating costs.”
Keith Dougherty echoed Brandon and Paul’s thoughts and suggested ways we can raise the bar at Pepper. “I would like to expand our use of modeling for all projects to allow for auto quantification of a project’s quantities.”
How does that benefit our projects? Keith explained, “By utilizing these models we are completing our work with higher accuracy and quicker response time, allowing for better information for our owners and designers… This is an exciting time in the preconstruction world, as we are right now changing the future of how our industry will work.”
High performance and sustainability
Sustainability is not going away, and in fact, we’re evolving the conversation from talking about recycling and waste management to the health of our buildings and their occupants.
Susan Heinking is passionate about this topic and has big ideas for where she would like to see our industry head. “For me, it starts with the impact construction has on our environment, and thus our health. I’d like to see construction companies implement measures with the goal of reducing our impact, whether required or not, because it’s the right thing to do.”
She goes on to explain, “As contractors, too often we fall into a trap of thinking that we’re not the planners; we’re the doers. Change starts further upstream. But that’s not true.” Thanks to Susan’s efforts to educate our staff at Pepper, we’re starting to incorporate conversations about high performance and sustainability into more and more projects because there are things we can control, like reducing idling, minimizing onsite storage and suggesting alternative, healthier materials.
Environmental
Because of our specialized expertise in environmental technologies, several of our subcontractors are educated in the identification of many environmental hazards, and they have been instrumental in stopping work when potential hazardous building materials are identified.
While some situations are unforeseen, Mike Grant suggests there is room in our industry to be more educated about how to anticipate and better plan for these conditions. “We could certainly benefit from integrating environmental services into the overall project, as well as engaging environmental expertise earlier.”
Virtual construction
From improvements in existing hardware and software, to new technology and an increasing number of new adopters, 2016 was a big year for technology in the construction industry. The options are becoming endless – and for some can quickly become overwhelming.
Jennifer Suerth explains, “As technology implementation grows, the amount of data increases along with it. Data management and analytics will play a more vital role in our projects and operations in 2017, and there is definitely room for improvement. Information overload is a real concern in our industry.”
So where should we focus in 2017? Jen believes the biggest opportunity related to technology and construction is predictive analytics. “Predictive analytics can be directly tied to safety and quality, an aspect of construction that is extremely important, and yet many virtual design and construction groups are still struggling to understand how they can do more to improve in those areas.”
“As virtual design and construction staff, we need to further enable our project teams to be hands-on with the technology (preconstruction, project management and field staff),” shares Mike Alder. “[We should] explore with them how we can improve conceptual estimating and use virtual reality to assist with safety and quality planning.”
Kevin Stipp’s resolution was about addressing one of the biggest challenges we are faced with right now – workforce shortage. “How can we use technology to help with that shortage? Whether it’s mobile technology, the assistance of UAVs, printing materials or moving toward prefabricating different systems and in higher quantities, we need to find ways of doing more, or even the same work, with less.”
The technology is there. We have subcontractors who are talking about it now - but not that many. So what does that mean for 2017? Kevin explained, “Our subcontractors don’t know what technology exists or where it’s headed, and we will need their help in finding solutions. 2017 needs to be about educating and training the workforce in the use of technology.”
Workforce
That leads us to our last topic - construction site supervision and trade work – where all of our plans and ideas converge to be implemented and proven in the field. As such, our workforce leadership’s responses covered all aspects of a project.
“I'd like to see us focus on training, collaboration, empowerment, innovation and communication,” shared Jeff Wojcehowicz. “We should have complete buy-in that allows everyone to feel like their suggestions matter.”
Quentin Young agreed with many of Joe’s thoughts: “I’d like to see us strive to become less encumbered by our past practices and welcome new approaches to different challenges.”
He added, “I’d like to see quality become a more prevalent concern and part of our daily plans. I’d like to see virtual construction and modeling continue to become more commonplace on each project, not just the larger ones, and I’d like to see our workforce continue to grow, becoming more capable in increasingly challenging projects.”
Scott Kennedy applied his New Year's resolution to both internal and external customers: “Utilize the latest technology in the office and field to increase safety, productivity and quality…”
He finished with an insightful wish, “Continue a positive and enjoyable work environment for our employees, their families, our customers, our suppliers and our subcontractors.”
On the surface it doesn’t seem like a statement to make in a New Year’s post for our industry, but he’s right. Construction is hard work, and it’s also fun. Our teams take pride in building and enhancing our communities, and it’s important that we create a safe, healthy and respectful environment for them every day.
What's next?
These thoughts are only snippets from the responses that I received from our team. The themes that emerged include better and earlier collaboration, communication and integration, with a focus on transparency and technology.
I know – all concepts we’ve heard before, and all easier said than done. But we’re not giving up. We’re exploring ways to tackle these challenges one step at a time.
In the ensuing months we’ll be sharing our ideas, what we learn, what we’re trying and any progress as it unfolds – some of which our team touched on today. I encourage you to follow us, learn from us and talk with us as we push our industry to be better.
About the Author
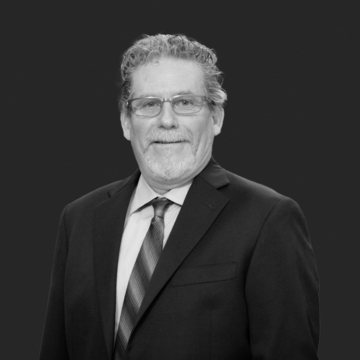