Future In Focus, Healthcare
Future in Focus
"The healthcare industry has served as a model for others to follow through strategies that create healthy environments, like Evidence Based Design. Healthcare employees, processes and facilities have been greatly impacted by COVID-19 -- and eventually everyone will once again turn to healthcare to see what they do." – Susan Heinking, Vice President, High Performance and Sustainable Construction
Over the past few months, we've worked with clients on spaces critical to their operations, while other work was placed on hold. Right now, there seem to be more questions than answers. Will there be a W-shaped recovery, or second wave, or have we already seen the worst? When it comes to their projects, healthcare providers are closely monitoring the situation as it unfolds, and systems are beginning to talk about fundamental changes they expect to make to be pandemic-ready.
Current healthcare construction outlook
Looking ahead, many architects and industry organizations are talking about how the pandemic will re-shape the future of healthcare. Do hospitals need to offer all services in all locations? Will there be more healthcare system consolidations, or will more services move closer to patients? At the top of the list is the need for more flexibility in their facilities to adapt quickly to different needs as they arise.
What about the immediate forecast? Based on our own pipeline and conversations with clients and industry partners, here's what we're seeing in the Midwest:
-
Healthcare providers are re-thinking the design of MOBs after COVID-19. - Architects are finishing work that was already in design pre-COVID-19, but we're hearing new projects have slowed significantly.
- Healthcare providers that were in good financial position before the pandemic are choosing to proceed with priority projects, with little or no change to designs.
- Some renovations could be delayed as hospitals increase the number of elective procedures to catch up with pent up demand; they can't afford to give up the space right now. They may also decide to extend projects over multiple years to spread the cost.
- Major projects that were in programming or early design have paused as healthcare providers reconsider designs. For new construction, they're exploring what they can do to be prepared for the next pandemic or disruptive event.
- Projects such as Medical Office Buildings (MOBs) have been delayed, as owners redesign the spaces to fit a new way of working, with services like Telehealth, which are expected to become more standard. Telehealth could also affect where physical space is constructed by consolidating more services in the major hospitals, resulting in less space needed for office visits.
- When it comes to construction, we're seeing this service impact MOB designs by incorporating private work rooms for physicians to facilitate calls.
- Clients are not in a hurry. They're taking a step back and regrouping. The new timeline for projects moving forward is two years out.
The cost of healthcare construction
So far, our teams have not seen significant changes in pricing, with the past quarter reflecting work that was already in progress. We expect to gain a better idea of where the market is headed in the next three to six months.
Materials and Supply Chain |
One of the most significant impacts we've seen since the start of 2020 is on our supply chains. We are seeing longer lead times, and some materials are unavailable. For example, due to shutdowns, today we're unable to get specialty tile from Italy. Locally, there have been issues with receiving casework because the mills were shut down. To head off potential issues early, during preconstruction our teams are looking at where materials originate and working concertedly with architects and domestic manufacturers to ensure delivery. |
Manpower |
Manpower has remained constant. As we start to approach more normal levels of construction activities, with jobs that continued and those that were postponed coming back, we could experience manpower shortages again, like we did before the pandemic. The shortage could be compounded if those who have been unemployed elect to not return to the labor force. |
Competition |
The trade activity is a tale of two stories. Specifically, with MEP trades we're starting to see more interest, with 8-10 bidders. However, there is still a good spread in price, which indicates some companies are looking for work due to delayed and canceled work, while others still have a healthy backlog. This situation is not equal across all trades though; prices have remained consistent across most trades. |
Aside from these factors, we anticipate the cost of some spaces, specifically, technically-complex spaces like operating rooms, will likely increase slightly due to inflation and additional mechanical requirements. Consequently, the healthcare systems that historically incorporated the minimum requirements in their initial budgets have the potential to see the biggest cost swing.
Right now, there is a premium to add Ultraviolet lights (UV) in ductwork to help sanitize the air, and as its use becomes more common, we expect the costs to come down, similar to what we saw with LED lighting. Recently, we priced the addition of UV lights in an outpatient building at $2,000 per rooftop unit.
In a different scenario, for hospitals that are considering significant programming changes, like adding operating rooms inside an MOB, the cost per square foot of an MOB would increase significantly.
Bringing the future of healthcare construction into focus
"We're not biologists, but it is becoming more important that the design and construction community understands microbiology and how systems and materials work together in a healthcare setting," shares Heinking.
Evidence Based Design and High Performance features are expected to become even more important, with an emphasis on how air quality, density and materials work together. Consideration will be given to the following:
-
Daylight is an important feature in healing environments. - Ability to adapt a space for negative air
- Daylight for exposure to Vitamin D
- Sensors for operating doors, fixtures, etc.
- Density and increased outdoor air - 30 cubic feet per person
- Humidity levels kept between 40% to 60%
- Verification of ventilation performance with real-time monitoring of CO2
- Ductwork that incorporates MERV 13, HEPA filters and UV lights
Many providers have already taken extra measures. In addition to planning for surge capacity, what else can you do to prepare your buildings for the next event?
- Consider a certification that fits your business model; all include health considerations that support a pandemic-ready initiative. Going through the certification process allows you to prove out the measures that are in place through a third party.
- Explore streamlining your facility management process by conducting a Facility Condition Assessment. This will allow you to document current conditions, target the activities that need to be addressed first and appropriately budget for specific needs.
- Partner with an MEP contractor to help evaluate your MEP systems. There is a lot of discussion about incorporating UV lights and making changes to mechanical systems. Your contractor can help interpret how design changes could affect the systems' performance and the solution that is right for your building.
- Reference a healthy materials database, like Mindful MATERIALS, to explore alternative, healthier options, like antibacterial coatings.
Finding efficiencies through Lean Construction
Director of Continuous Improvement Heather Siemers has spent most of her 20-year career working in healthcare environments, first in project management, then quality management, before transitioning to her current role. She believes the future of healthcare construction can be greatly improved through Lean Construction, but it will require commitment by the owner.
"When the owner makes Lean a priority, it results in a higher level of adoption by the rest of the project team." But Siemers concedes it takes a lot of work. "The most committed clients struggle with helping facilitate the process. It takes time, and right now they're already maxed out."
With strained resources, where should owners spend their time to make the biggest difference?
Siemers suggests the following to start: "When defining the True North and establishing the Guiding Principles at the beginning of the project, challenge user groups to think about what they would need if something were to happen again. By identifying that need as one of the project values, the team will make a concerted effort to incorporate it into every process and decision. So, for example, if the space needs to be adaptable, that value should inform the Target Value Design process, so the budget includes those design elements that make it adaptable."
Leveraging technology to advance the work
Technology can help hospitals prepare now for future work. Jennifer Suerth, vice president of technical services in Illinois and Wisconsin, suggests while the census is down, hospitals should consider capturing existing conditions with laser scanning and drones. That way, when renovations are ready to start, they'll have the data that can otherwise be challenging to access when occupied.
Technology has also found efficiencies for work in progress. For example, on a recent operating room project in Indiana, a virtual mock-up allowed the project to proceed when the planned physical mock-up was going to delay it. Virtual mock-ups are becoming more broadly used because they help facilitate the review process with doctors and nurses, whose feedback is critical but whose time is very limited. Additionally, since every detail (soap dispensers, outlets, equipment, etc.) is shown to scale in the virtual model, staff can see how the design could impact a patient – and even move the equipment to test the space. In addition to these benefits, our clients also realize cost savings. Virtual mock-ups have become more valuable now with COVID-19.
In Illinois we found ourselves limited in the number of people who could walk through the hospital space on a bid walk. The solution: One person walked through the space with a 360-degree camera. He attached the photos to the floorplan for our team to tag with comments for everyone to see. The 360 photos gave everyone the same vantage point and created a conversation. This practice has since been used for bid walks on other projects.
What's next in healthcare construction
Director of Virtual Construction Mike Alder has applied technology solutions on more than $2 billion in healthcare construction in Indiana, and he has worked in all types of healthcare spaces. In January, Alder attended a conference, where he observed Autodesk CFD, which is used by engineers to map how air flows through a space. With Pepper's focus on high performance and healthy solutions, he saw an opportunity to apply it to the construction process.
"I thought if we could create a visual of people in the space and the air flow around them, maybe it could help clients make decisions from a well-being perspective – for both patients and staff." -- Mike Alder, Director of Virtual Construction
Alder worked with Autodesk to test it on a hospital project. After reviewing the visuals of the simulation, our quality team saw even more potential. If we could simulate the air flow through the ductwork before it gets to the space -- and not as designed but as it was installed -- we could understand how potential field changes impact air flow.
Indiana's Director of Quality Management Ben Dykstra helps project teams plan the construction details through pre-installation coordination meetings. "Our role is to plan and coordinate the work so it is installed correctly. Sometimes that means making modifications to the design to improve how it is constructed, which is why we include the engineer in the process. A platform like this would allow us to verify the changes we want to make in advance – and to test them in a virtual environment."
The application is still being evaluated after our initial trial. As our team considers how we help clients visualize the performance of their space, the potential for this idea became more relevant with COVID-19.
Heinking is already thinking ahead: "When I heard about the solution, I thought about the next evolution and the ability to model particulate matter based on different types of filters, to visually see what's in the air and how it's flowing through the space and exiting. It could be used for design decisions and to prove the system's performance."
The pandemic has underscored the need for healthier spaces. Dykstra and Heinking agree the future of healthcare construction is about understanding the relationships between systems and materials and how they can be designed to create healthier environments. It's not a task that should be left to architects and engineers alone, but a commitment that should be shared by those installing the work as well.
We don't have all of the solutions today, nor can we predict what will be needed in the future. But we believe it will take new solutions like this to ensure healthcare systems avoid becoming overwhelmed when creating healthier environments that, in turn, allow for a higher level of care.
This blog post is part of the Future In Focus series, which analyzes the decision to proceed, as well as the creativity and tools to wisely manage your project. Experts from across the company are weighing in so you can start to sort through all the unknowns and make the most informed decisions possible. We encourage you to subscribe to our newsletter to receive updates.
SIGN UP TO RECEIVE UPDATES
About the Authors
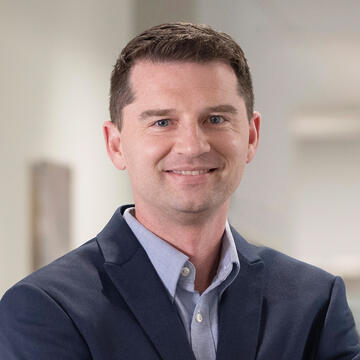
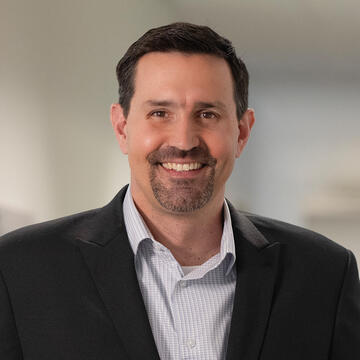
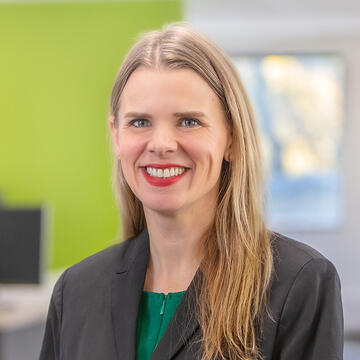
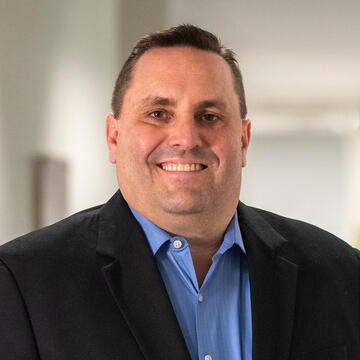
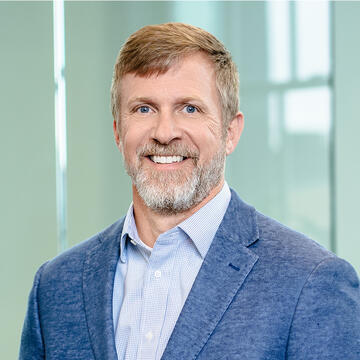
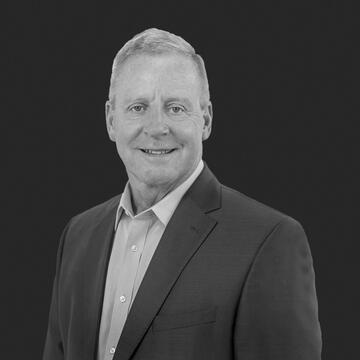

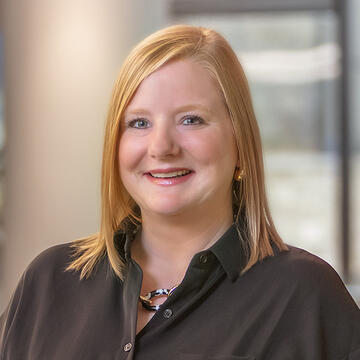