High performance & sustainability, Lean Construction, Safety
In the midst of this pandemic, it's hard to think too far into the future. What was important two months ago may not be our top priority today. But one truth remains even more relevant, and that's how our environment affects us. Since we spend up to 90% of our time indoors, a building can impact our health and well-being.
There is a lot of discussion right now about how work-life will change when people eventually make the transition back to their respective workplaces - hopefully in the near-term. Naturally, it's predicted that workers will have a heightened awareness of the risk of infectious disease transmission and the building's role in their health. More attention will be given to density and air quality, among other factors.
Buildings that are managed poorly can be vectors for disease, by concentrating indoor pollutants. Alternatively, buildings can also help when managed properly through Cx, indoor air quality monitoring and improving ventilation. As contractors, we have the opportunity to establish high quality indoor environments and set the stage for the level of air quality the building provides.
Historically, contractors have followed the design industry's lead - building what gets specified without offering ideas. But times have changed. The partnerships that we have today give us more opportunity for contractors to make a difference by changing how spaces are built.
Pepper’s long-standing Nothing Hits the Floor program is designed to deliver a cleaner indoor environment, starting during construction. A couple years ago I wrote a blog post about our program, and it's worth revisiting the conversation again - in an effort to make our best practices common practice.
Consider our healthcare clients who are on the front line: hospitals are among our most sensitive jobsites and as such, require extra measures to maintain proper indoor air quality. We follow Infection Control Risk Assessments (ICRA) and Interim Life Safety Measures, which can include the use of HEPA filters and coveralls. For cleanrooms, anti-rooms are used to sanitize materials before they are installed, and workers are trained, badged and suited up before they are allowed inside the space – throughout construction and not just in the final days.
These owners understand a messy and unorganized jobsite can indicate the potential for issues through increased safety exposures, quality control gaps, inefficient workflows and poor air quality. Any dirt and debris onsite can end up in walls, under flooring and in the systems that operate the building – and into the air that is breathed by the end user. The more dust and debris that remains onsite, the more likely it will be trapped in the building upon completion.
A messy jobsite is also more likely to put the tradesperson in the position of making a choice about being productive, being safe or taking quality shortcuts. To help prevent these types of decisions, our Nothing Hits the Floor program is designed to keep the jobsite organized and well-managed by addressing safety, quality, productivity and performance at the same time. Through a seven-step process, the goal is for all field personnel to keep work areas clean and for all materials to be mobile and installed as close to their delivery dates as possible. More importantly, by enforcing a clean, lean site, our clients receive a cleaner, healthier space at turnover.
Nothing Hits the Floor has been an effective program for us, and we're inspired to do more. This is a good time for us to re-examine how we build - because every client deserves an environment that improves their quality of life.
About the Author
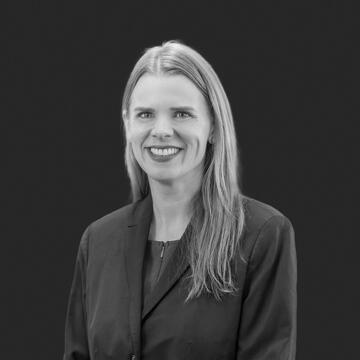