Credits
Creating a global connection with strategic innovation and earned trust
When Pepper first began working with the team from Stevanato Group, an international company based in Italy that had selected Fishers, Indiana, as the site for their new manufacturing plant and North American headquarters, we quickly realized that the project’s success could be determined by our ability to successfully bridge an ocean of differences. Challenges involved everything from language and cultural differences and construction acronyms, regulations and processes to units of measure, pricing and how and when to engage trade partners.
Add on a broad scope and the project’s aggressive timeline, and one thing becomes clear as glass: every day and every decision will matter.
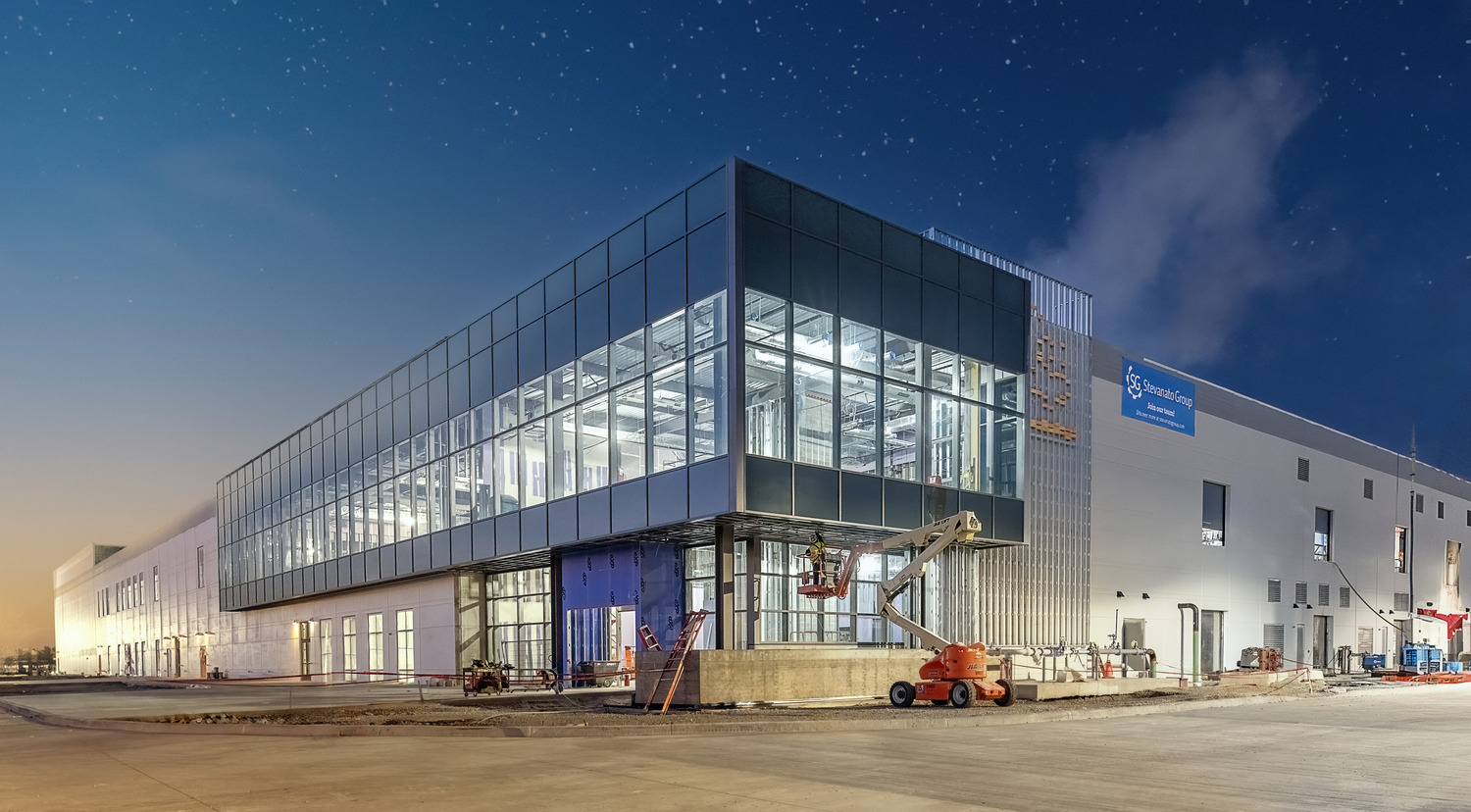
Chances are, if you received the COVID vaccine, it came in a vial made by the Stevanato Group. Approximately 80% of the vaccines were delivered through their technology. It’s a unique product where the packaging is never opened once it is sealed until it reaches its destination.
After many discussions, we came to a mutual conclusion: To help Stevanato Group build effectively in our backyard, we had to go and visit theirs. So, the Pepper team boarded a plane bound for Italy to better understand what Stevanato Group does and how they do it, their priorities and how to help them adjust to both the business landscape in the United States and the construction industry in Fishers. The opportunity to see an active facility in person allowed us to better visualize what we would be building, ask specific questions of the Italian engineers, and hammer out any outstanding issues from design, construction, technical and legal perspectives. The plan was to meet all day and enjoy dinner together each night. Those dinners are where we really started to connect.
Building a partnership
While the six-hour time difference between Piombino Dese, Padua, where Stevanato Group's headquarters is located, and Indianapolis, where the Pepper team is based, could have been a challenge to keeping everyone on schedule, we established processes that worked to our advantage. Virtual meetings early in the morning helped to set the day’s priorities for the US team. When we returned to work the following day, partners in Italy had already responded to questions and done additional work, which essentially allowed us to operate efficiently around the clock.
It’s all about timing and flow
Because of the value that having an EZfill® manufacturing facility available in the United States would provide, we knew that the project schedule would be aggressive.
The top priority was to get the first production line up and running as soon as possible. In addition to manufacturing space, that required supporting lab space as well as specialty mechanical and electrical rooms, clean rooms, airlocks and other spaces. As procurement and essential design changes to the production lines began to shrink our window for construction, we quickly realized that we needed to take a more innovative approach to give Stevanato Group the spaces they needed when they need them, while still having adequate construction time to complete the entire building.
To accomplish this, we needed to complete construction in the middle of the building, and then create a pathway that would allow the Stevanato Group team to directly and safely access the space to set up their labs and instrumentation and install and calibrate the production lines with very complex, cutting-edge machines. At the same time, construction tradespeople were working on the other side of the walls to continue construction on the rest of the building.
The entire process was a significant departure from how these facilities are typically built and required flexibility and steadfast dedication to the details every day.
The benefits of technology
-
Two full-time BIM and MEP coordinators located on-site were critical to the team’s success. Efficient work in the field would have been much more difficult, if not impossible, to complete at the pace required.
- Drones helped monitor weekly earthwork progress through a cut-fill analysis, which was particularly beneficial when filling a large pond on the property during phase two.
- 360 photos were taken weekly, providing complete photos of every room in the building as it progressed from an empty space to framing, mechanical rough-ins and drywall.
- Pepper’s underground utility damage prevention (UUDP) process helped safely map the utility infrastructure for the entire 70-acre Life Sciences Park. A GPS mapping tool was used during the potholing process yielding a precise as-built record of the underground utilities that will be useful for the Stevanato Group's future needs, while also benefitting the City of Fishers and other contractors working on the site. Electrical duct banks running beneath the slab are 30 feet wide and 10 feet deep with hundreds of conduits running through them. Knowing where they are and where the 95 miles of different conduits go was critical to our construction success and will support the site’s ongoing operation.
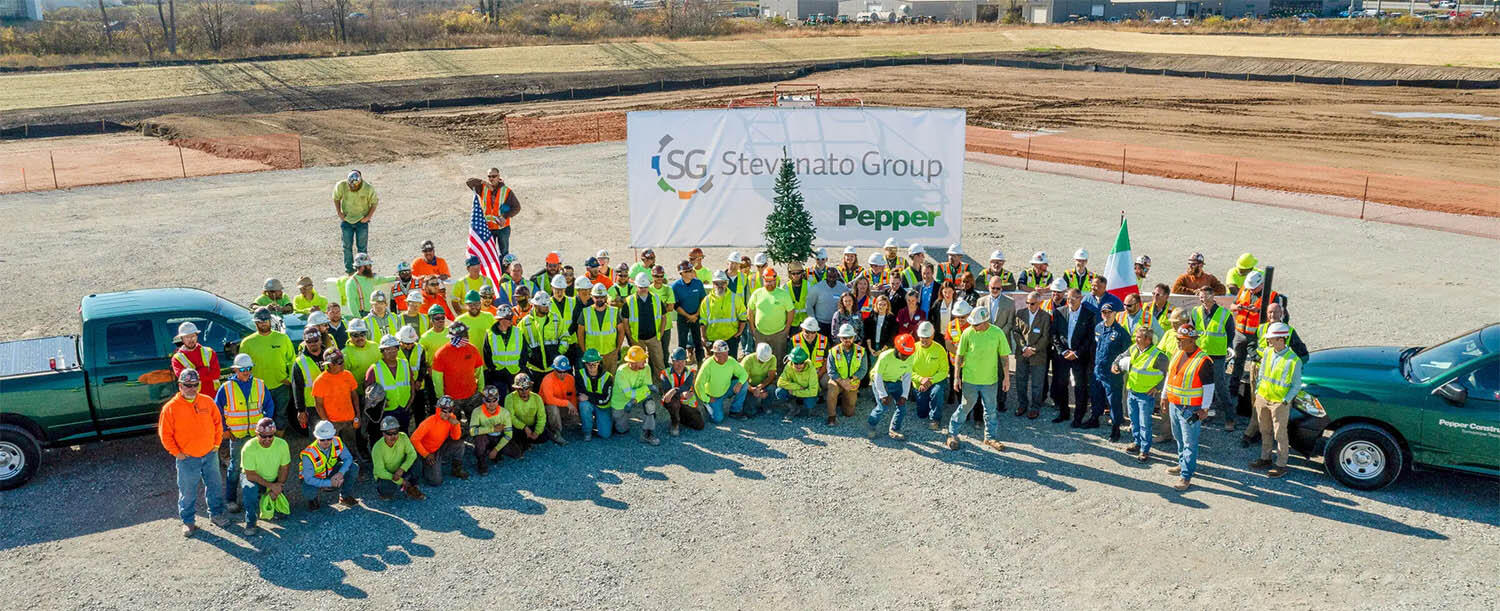
Saluti! Cheers!
While we still have more on our plates before the project is completed in 2024, the team is sharing an undeniable sense of contentment and satisfaction.
From Stevanato Group’s seat at the table, the new facility fills a critical need to produce and deliver vials to U.S.-based pharmaceutical companies faster and more efficiently. The Fisher’s location is conveniently positioned to deliver their products across the country. In addition, the new Life Sciences and Innovation Park that they are helping to anchor will help to attract additional specialty workers to the area and further enhance Indiana’s bragging rights as having the third highest concentration of biopharmaceutical jobs nationally and being the second largest exporter of life sciences products in the U.S. [source: Indiana Economic Development Corporation - IEDC]
From the Pepper team, we consistently hear how proud our people and partners who grew up locally are of what they’ve been able to bring to their “hometown”:
- A 36-acre jobsite with construction opportunities for more than 450 tradespeople
- Watching what they’d always known as a cornfield and pond transform into a worldclass science and technology facility
- The largest project performed by Pepper’s Self Perform Group concrete team (25,500 cubic yards with 1,000 tons of rebar)
“At the heart of this project is the type of science, technology and advanced manufacturing work that we see as Pepper’s next wave of growth,” said Dan Peddicord, President of Pepper in Indiana.