Safety, Quality
For several years now, we’ve been trying to inspire our industry to feel empowered to make the right decisions in favor of safety. We want our people to speak up when they see a better and safer way of completing a task. A while ago, I was encouraged when I received some positive feedback from one of our foreman. He shared his perception of Pepper – that we mean what we say. We don’t just talk about safety; we expect it. We support it and value input from everyone.
Then, he offered a great suggestion: It would be nice to have a new hire safety orientation for field staff to learn more about the company and our commitment as an organization. At the time, all we offered new field employees were job-specific safety orientations.
A simple suggestion leads to transformation
At Pepper, we’ve always understood that safety and quality go hand-in-hand, but that message hasn’t always been incorporated into how we plan and manage our projects. As we've implemented lean principles over the past few years, we’ve made more of a concerted effort to work together - and to involve everyone in our continuous improvement process.
So after taking the suggestion to heart, the first person I approached about developing new onboarding training specifically for field staff was Director of Quality Management Heather Siemers.
From there, we approached Group Superintendent Quentin Young to incorporate productivity into the discussion, as well as Self Perform Superintendent Jason Johnson.
Opening up two-way communication
Initially designed as a one-hour presentation, we quickly revised it after the first session turned into nearly two hours of conversation.
We start by sharing information about Pepper, like our organizational structure, projects we’ve completed and the types of work we perform.
Then, we talk about our objective: to safely build high quality projects productively. We share the resources that we have in place to help them achieve this goal:
- Plans
- Tools
- Materials
- Training
- Leadership support
The last bullet sets up the rest of the presentation, where we talk about different risks and how we want them to feel empowered to speak up, stop work and make decisions. And reinforce that we have their backs. This is the part of the presentation where they start to respond.
A safer and more effective path to quality
With workforce shortages and advances in technology, continuous improvement efforts are more important than ever. Our industry is in a position of doing more with less and accelerating activities to new levels. If we don’t find better ways and involve everyone in the process, we’ll end up sacrificing the safety of our people and the quality of our work.
Our tradespeople are out making choices on our jobsites every day, and we can’t micromanage. There are risks associated with every path they take. It’s our job to provide the conditions that minimize those risks – the right tools, materials and equipment.
Our onboarding training is about arming them with answers. We’re educating them about how quality, safety and productivity work together so that when faced with a decision, they find the answer that works for all three.
The challenge flag
In football, when a coach disagrees with a call, he throws a flag to challenge the decision. During the training, we give this analogy and distribute red flags to each person. We want to empower them to stop work and challenge a decision at any time.
The red flag was a symbol until one day one of those flags was used on Quentin’s job. His team was working to bring a custom piece of equipment through narrow, existing structures. Not only was it challenging, it also presented safety concerns and was causing a delay in the schedule.
“We were spending a lot of time and muscle trying to put the equipment in place… when a red flag came whizzing by my head. One of my guys threw the challenge flag. I didn’t expect anyone to actually use the flag, and it certainly got our attention,” explains Quentin.
He goes on to share how everyone stopped what they were doing and listened to the tradesman explain his idea for an easier way of getting the job done. “After that, it was like everyone worked together to modify the plan, then the equipment was quickly installed and the project was back on track.” Equally important, that tradesman felt heard and empowered.
From strains to gains
Since we implemented our new hire orientation, we have seen several success stories come from the field. One simple, yet significant suggestion was to add pick points to our trash buggies so a forklift can be used to move them. Without the forklift, it is time intensive, manual labor and the cause of many lacerations, strains and sprains. The suggestion of the pick points improved both productivity and safety. It was a win/win for both our company and our tradespeople.
On another jobsite, our concrete guys ran into bad soil. The engineer wanted us to dig deeper, which would have created unsafe conditions. Our team stopped work and scheduled a meeting with self perform and safety to find a more viable solution.
Their solution of using a pump truck with a hydraulic arm and a storey pole achieved better results than the original recommendation of digging deeper. It provided better quality control, was safer and improved productivity.
More eyes and ears
From a quality perspective, empowering our tradespeople to speak up has multiplied the quality control on our projects.
“We don’t expect everyone to be experts about everything, but with the years of experience that our trades bring to our projects, they know when something doesn’t look right. They know when shortcuts have been taken. So what they can be is another set of eyes and ears in the field. We ask our tradespeople to take another look before we pour concrete or hang the drywall,” explains Heather.
Our guys are starting to speak up when studs have been notched for mechanical and electrical work – or to ask us to verify work that doesn’t seem right. They’ve even offered suggestions for detail changes that we are able to run by the design team.
It's about people
Tradespeople add valuable input, which translates to our work. And their influence is spreading to others – other trades and even strangers.
One of my favorite stories happened recently. One of our foreman shared that he was driving at night and saw an older lady on a scooter in a parking lot - but just barely. He pulled over and gave her his safety vest so that she would be visible and safe to other drivers. So if you see a woman on a scooter wearing a Pepper safety vest…that’s why. To us, safety is about more than our work; it’s about people.
About the Author
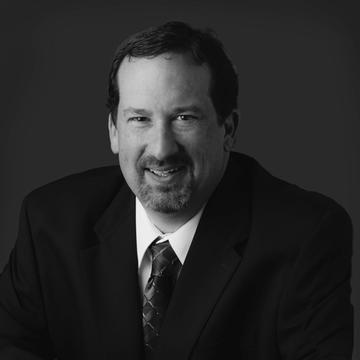