Plan for Flexibility
Purdue’s new Flex Lab Facility needed to be flexible enough to accommodate new trends and technology for years to come – all within an established budget. Extensive preconstruction efforts – a process that wouldn’t have happened under the traditional design-bid-build process – allowed the construction team to be highly collaborative while building a facility that meets the University’s current and future needs.
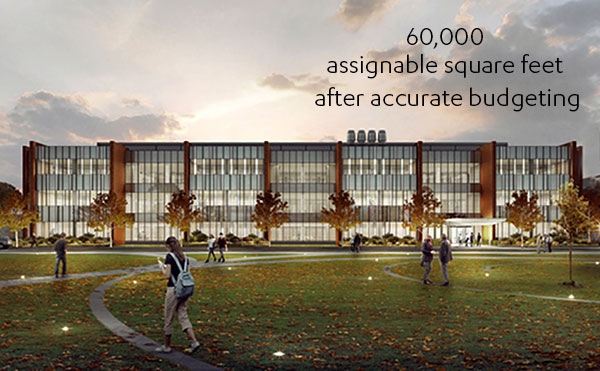
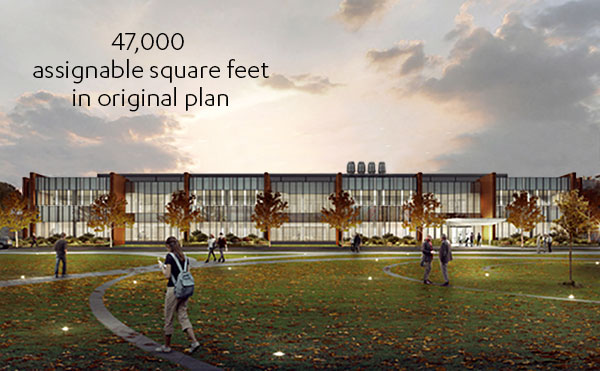
The preconstruction work resulted in significant immediate and long-term savings. Immediate savings included several options that achieved the same look and performance for less, such as ceramic tile instead of terrazzo flooring and an alternative curtainwall design. In addition, a site analysis shifted the building footprint and reduced upfront costs associated with sitework. These changes allowed the University to reallocate dollars to other spaces within the building. Long-term, Pepper's extensive expertise with science and research facilities provided accurate budgeting and helped Purdue realize they could add an additional 13,000 assignable square feet to the facility, a 28% increase that included a third floor.
A rigorous structural analysis considered seven bigger-picture factors like how a design choice would impact cost implications of winter conditions, or how it might affect floor-to-floor heights, which could limit equipment choices. With the facts laid out before them, the University could choose the option that best serves today’s needs, while accommodating future changes to the space.
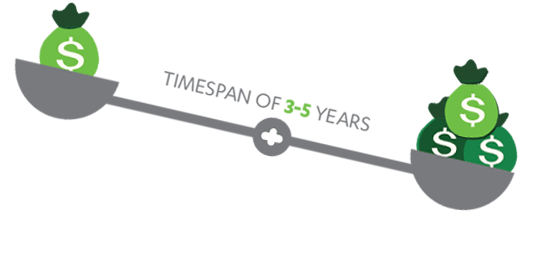
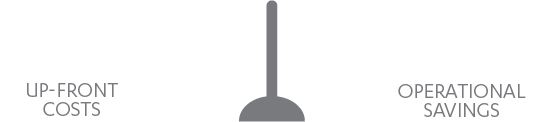
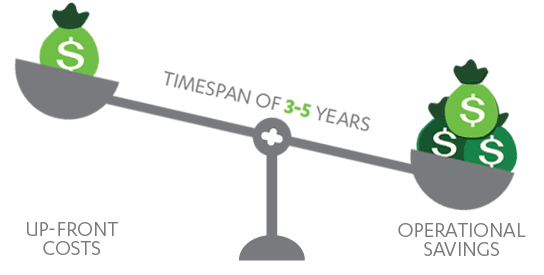
The preconstruction process also enabled the University to weigh energy consumption and long-term operational savings against upfront costs.
“The growth of the Purdue University College of Engineering made a new multidisciplinary research facility necessary. The stated scope for Flex Lab was to provide 60,000 assignable square feet, but during the programming phase, it appeared the budget would only support 47,000 assignable square feet. By using the CMc delivery method, we were able to achieve our original scope goals.”
Robert Smith
Director of Construction, Purdue Physical Facilities
A Common Vision
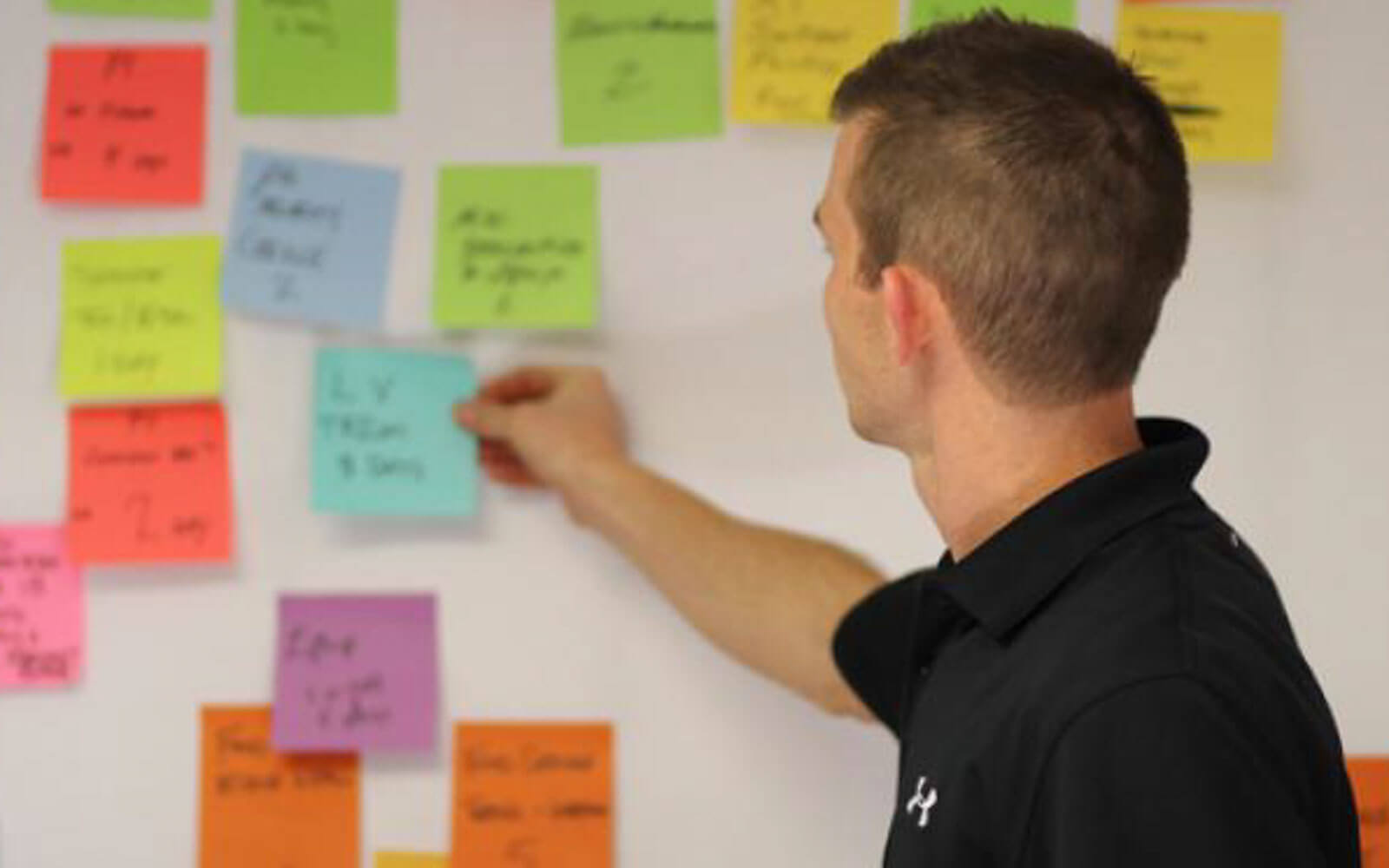
A true CMc environment encourages high levels of collaboration and transparent communication during design, preconstruction and construction. The team used pull-plan scheduling to streamline the process, establish a common vision and increase accountability between team members. Pull planning was a valuable meeting strategy, identifying project milestones and preventing issues later in the project.
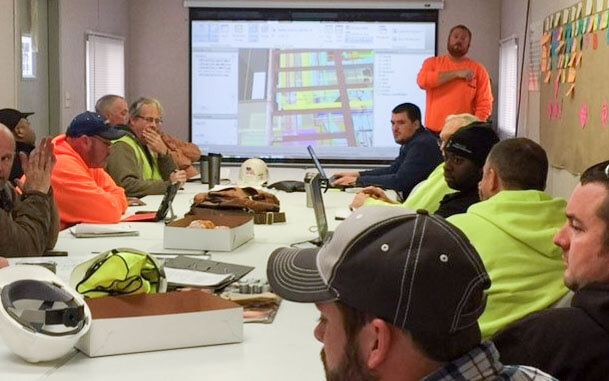
Perhaps one of the best examples of this holistic approach was the design coordination process. With winter weather looming, the team soon realized it was imperative to begin concrete work as soon as possible. They accelerated the preconstruction process so concrete bid packages could be obtained and selected quickly. Pepper volunteered to help lead the design coordination process, facilitating upfront conversations and idea generation from the designers, the structural engineer and the owner. Solutions were efficiently integrated and the schedule was maintained.
Focus on Inclusion
Purdue’s commitment to supplier diversity is recognized as one of the premier programs in the country. Implementing the CMc method allowed the team to not just meet – but to exceed goals for diverse participation in the project.
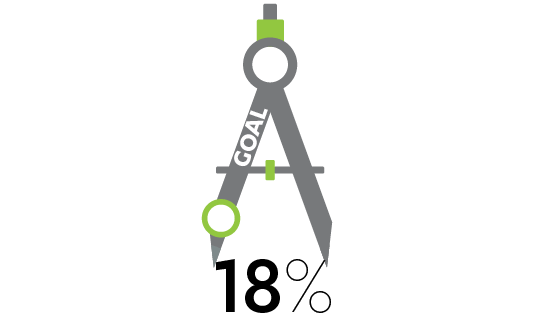
Pepper/Davis set a diversity goal on the Flex Lab Facility to reach 18 percent minority, women and veteran-owned businesses (M/W/VBE). With the project nearing completion, the team actually achieved more than 22 percent M/W/VBE participation. How? By leveraging a close working partnership with Purdue’s Supplier Diversity Program that included multiple outreach and bid informational events and a speaking engagement with the Indiana Subcontractors Association. Beyond the project’s success, the success of Pepper’s joint venture partnership with Davis led to multiple speaking engagements with the North Central Indiana Business Conference to discuss the power of joint venturing and mentoring with minority businesses.
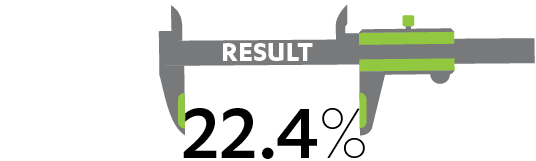
Visualize the Plan
The plans developed during preconstruction evolved as construction progressed. The team embraced technology as a tool for planning and communicating with trades, including 4D scheduling to illustrate phasing and logistics. The 4D model facilitated discussions with field personnel on sequencing and site safety. Temporary handrails and hole covers for fall protection were incorporated into the model. To ensure all of the trades understood expectations for how to use the model, on-site training demonstrated the software and its capabilities.
What's Next?
Purdue has selected Davis/Pepper to collaborate on their next project – the Agricultural and Biological Engineering Building. The project will encompass approximately 125,000 assignable square feet of new space and renovate approximately 37,000 assignable square feet of the existing facility. Once complete, the state-of-the-art facility will support cell and molecular biology, wet chemistry, bio-process equipment, computing research, teaching and support spaces.
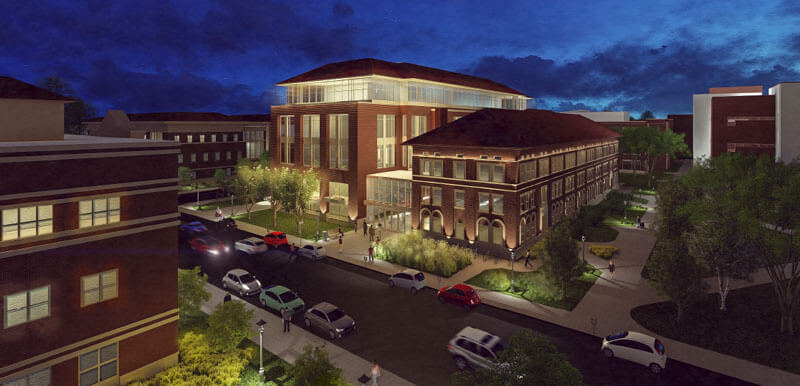
Purdue University Flex Lab Facility
Location: West Lafayette, Indiana
Owner: Purdue University
Joint Venture Partner: Davis & Associates
Architect: Jacobs/Ennead
Photography: Studio 13 Photography